OLED backplane structure and OLED backplane manufacturing method
A manufacturing method and backplane technology, applied in the field of OLED display, can solve the problems of limited effect, large conduction resistance of OLED display, high energy consumption of OLED display, etc., and achieve the effects of reducing energy consumption, eliminating metal annealing treatment, and simplifying the manufacturing process
- Summary
- Abstract
- Description
- Claims
- Application Information
AI Technical Summary
Problems solved by technology
Method used
Image
Examples
Embodiment Construction
[0044] In order to further illustrate the technical means adopted by the present invention and its effects, a detailed description is given below in conjunction with the preferred embodiments of the present invention and the accompanying drawings. It should be noted that the accompanying drawings in this application are only schematic diagrams. Unless otherwise specified, they do not mean that the actual thickness ratio, flatness, and shape of each film layer are the same as those shown in the drawings. Restriction, the actual product may be different from the schematic diagram, for example, the shape of the hole and the shape of the combined part of each film layer will be different from the schematic diagram, which can be understood and known by those skilled in the art. The description of the sequence of process steps and the structure of the film layers in this application only represents the sequence and relative positions of the steps and the film layers directly related ...
PUM
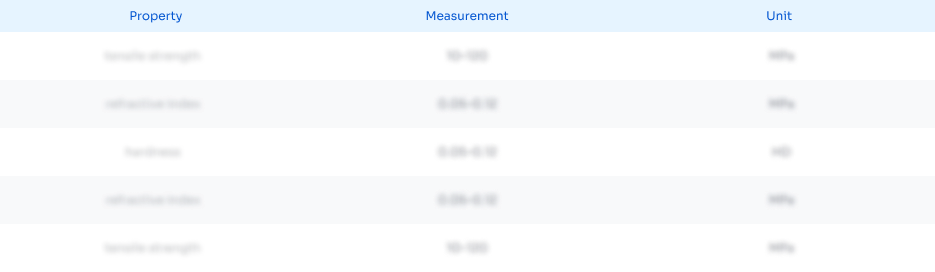
Abstract
Description
Claims
Application Information

- R&D Engineer
- R&D Manager
- IP Professional
- Industry Leading Data Capabilities
- Powerful AI technology
- Patent DNA Extraction
Browse by: Latest US Patents, China's latest patents, Technical Efficacy Thesaurus, Application Domain, Technology Topic, Popular Technical Reports.
© 2024 PatSnap. All rights reserved.Legal|Privacy policy|Modern Slavery Act Transparency Statement|Sitemap|About US| Contact US: help@patsnap.com