Method for catalytic pyrolysis of high temperature coal tar with iron oxide scale and magnetite
A high-temperature coal tar, catalytic pyrolysis technology, applied in catalytic cracking, cracking, petroleum industry, etc., can solve the problems of short service life of catalyst, easy coking of catalyst, difficulty of industrialization, etc., achieve high activity, good application prospect, easy Achieved effect
- Summary
- Abstract
- Description
- Claims
- Application Information
AI Technical Summary
Problems solved by technology
Method used
Examples
Embodiment 1
[0014] Embodiment 1: Weigh 1g of iron oxide scale (containing 30-100% of ferrous oxide, from Maanshan Iron and Steel Co., Ltd.) and 1g of magnetite (containing 70-100% of ferric oxide, from Maanshan Iron and Steel Co., Ltd.) Mix it as a catalyst and put it in a fixed-bed reactor, then raise the temperature of the catalytic cracking reactor to 600°C under an inert atmosphere, and continuously add 0.2g of coal tar at this temperature, and the coal tar is catalytically heated in a nitrogen atmosphere of 100ml / min. untie. The tar condensed from the catalytic pyrolysis of coal tar is collected through a constant temperature cooling tank. The collected modified tar was analyzed, and 77% was light tar, of which 12% were fatty compounds, 61% were aromatic compounds, and 27% were phenolic compounds.
Embodiment 2
[0015] Embodiment 2: Weigh 1.2g of iron oxide scale (30-100% containing ferrous oxide, from Maanshan Iron and Steel Co., Ltd.) and 0.8g magnetite (containing 70-100% ferric oxide, from Maanshan Iron and Steel Co., Ltd. Company) mixed as a catalyst and placed in a fixed-bed reactor, then the temperature of the catalytic cracking reactor was raised to 550°C under an inert atmosphere, and 0.2g of coal tar was continuously added at this temperature, and the coal tar was carried out in a nitrogen atmosphere of 100ml / min Catalytic pyrolysis. The tar condensed from the catalytic pyrolysis of coal tar is collected through a constant temperature cooling tank. The collected modified tar was analyzed, and 72% was light tar, of which 8% were fatty compounds, 63% were aromatic compounds, and 29% were phenolic compounds.
Embodiment 3
[0016] Embodiment 3: Weigh 1g of iron oxide scale (30-100% containing ferrous oxide, from Maanshan Iron and Steel Co., Ltd.) and 1g magnetite (containing 70-100% ferric oxide, from Maanshan Iron and Steel Co., Ltd.) Mix it as a catalyst and put it in a fixed-bed reactor, then raise the temperature of the catalytic cracking reactor to 750°C under an inert atmosphere, add 0.2g of coal tar at this temperature, and carry out catalytic pyrolysis of the coal tar in a nitrogen atmosphere of 100ml / min . The tar condensed from the catalytic pyrolysis of coal tar is collected through a constant temperature cooling tank. The collected modified tar was analyzed, and 70% was light tar, of which 15% were fatty compounds, 65% were aromatic compounds, and 20% were phenolic compounds.
PUM
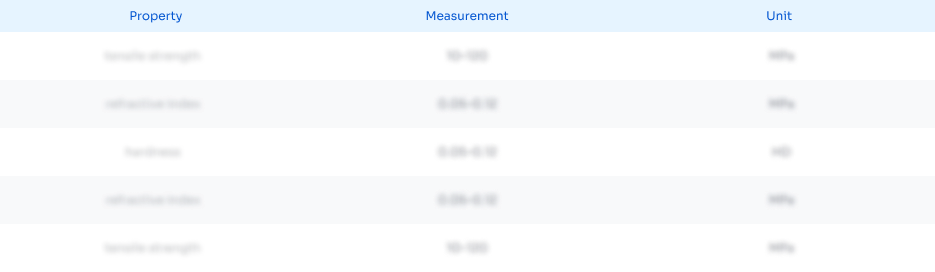
Abstract
Description
Claims
Application Information

- R&D Engineer
- R&D Manager
- IP Professional
- Industry Leading Data Capabilities
- Powerful AI technology
- Patent DNA Extraction
Browse by: Latest US Patents, China's latest patents, Technical Efficacy Thesaurus, Application Domain, Technology Topic, Popular Technical Reports.
© 2024 PatSnap. All rights reserved.Legal|Privacy policy|Modern Slavery Act Transparency Statement|Sitemap|About US| Contact US: help@patsnap.com