Fabricated prestressed concrete large-span frame system and construction method thereof
A frame system and prestressing technology, applied in girders, truss structures, and foundation structure engineering, can solve the problems of complex joint connection structure of prefabricated concrete, high repair cost of post-earthquake structures, and low construction efficiency, achieving increased Difficulty and procedures of construction, improvement of green construction level, strong replaceability
- Summary
- Abstract
- Description
- Claims
- Application Information
AI Technical Summary
Problems solved by technology
Method used
Image
Examples
Embodiment Construction
[0059] The prefabricated prestressed concrete long-span frame system proposed by the present invention can be found in figure 1 As shown, it includes foundation 5, prefabricated column 1, composite beam 2, floor slab 3 and external prefabricated wall panel 4. see figure 2 As shown, the prefabricated column 1 is a single-story or multi-story prefabricated one-section prefabricated reinforced concrete column without corbels, and the composite beam 2 includes the beam prefabricated part 2.1 at the bottom and the beam superposition of cast-in-place reinforced concrete at the top Layer 2.2, beam precast part 2.1 is the entire prefabricated reinforced concrete beam between columns, and the floor 3 is a prefabricated laminated slab, including the prefabricated floor slab 3.1 at the bottom and the laminated floor 3.2 of cast-in-place concrete at the top. Floor prefabricated slab 3.1 Prefabricated prestressed hollow floor slab, which can be prefabricated circular hole slab, prefabric...
PUM
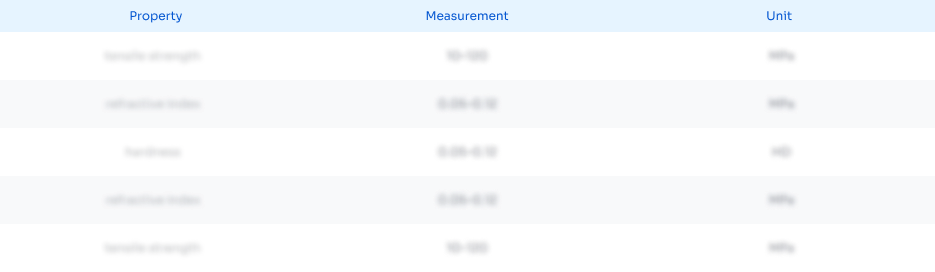
Abstract
Description
Claims
Application Information

- R&D
- Intellectual Property
- Life Sciences
- Materials
- Tech Scout
- Unparalleled Data Quality
- Higher Quality Content
- 60% Fewer Hallucinations
Browse by: Latest US Patents, China's latest patents, Technical Efficacy Thesaurus, Application Domain, Technology Topic, Popular Technical Reports.
© 2025 PatSnap. All rights reserved.Legal|Privacy policy|Modern Slavery Act Transparency Statement|Sitemap|About US| Contact US: help@patsnap.com