Preparation method for composite dry strength agent with high bonding strength
A dry strength agent, high bonding technology, applied in the direction of reinforcing agent addition, etc., can solve problems such as white water pollution, and achieve the effect of improving bonding strength
- Summary
- Abstract
- Description
- Claims
- Application Information
AI Technical Summary
Problems solved by technology
Method used
Examples
example 1
[0022]Add 80 mL of deionized water, 30 g of potato starch and 10 g of potato starch into a four-necked flask equipped with a reflux condenser, a stirrer and a thermometer, mix and stir for 20 min, then add 10 mL of 3-chloro-2-hydroxypropyl tris Methylammonium chloride and 6g of sodium percarbonate were mixed and reacted for 1 hour to obtain a reaction solution, and the pH value of the reaction solution was adjusted to 8 with a mass fraction of 10% sodium hydroxide solution, heated to 65° C. for 20 minutes, and cooled to obtain Self-made cationic starch, weigh 100g polypropylene and heat up to 160°C to obtain molten polypropylene, add 16g dicumyl peroxide, 30g maleic anhydride and 8mL acetone to the molten polypropylene, continue to keep warm and mix for 1h, and pour Extrude into a twin-screw machine to obtain modified polypropylene. Mix acrylamide solution with a mass fraction of 20%, dimethyl diallyl ammonium chloride and deionized water at a volume ratio of 3:1:2. In the rea...
example 2
[0024] Add 90mL of deionized water, 35g of potato starch and 15g of potato starch into a four-necked flask equipped with a reflux condenser, a stirrer and a thermometer, mix and stir for 25min, then add 11mL of 3-chloro-2-hydroxypropyltri Methylammonium chloride and 7g of sodium percarbonate were mixed and reacted for 1.5h to obtain a reaction solution, and the pH value of the reaction solution was adjusted to 9 with a mass fraction of 10% sodium hydroxide solution, heated to 70°C and kept for 25min, and discharged for cooling To obtain self-made cationic starch, weigh 150g of polypropylene and heat it up to 180°C to obtain molten polypropylene, add 18g of dicumyl peroxide, 35g of maleic anhydride and 9mL of acetone to the molten polypropylene, and continue to insulate and mix for 1.5h. And pour it into a twin-screw machine and extrude to obtain modified polypropylene. Mix acrylamide solution with a mass fraction of 20%, dimethyl diallyl ammonium chloride and deionized water at...
example 3
[0026] Add 100 mL of deionized water, 40 g of potato starch and 20 g of potato starch into a four-necked flask equipped with a reflux condenser, a stirrer and a thermometer, mix and stir for 30 min, then add 12 mL of 3-chloro-2-hydroxypropyl tris Methylammonium chloride and 8g of sodium percarbonate were mixed and reacted for 2 hours to obtain a reaction solution, and the pH value of the reaction solution was adjusted to 10 with a mass fraction of 10% sodium hydroxide solution, heated to 75° C. for 30 minutes, and cooled to obtain Self-made cationic starch, weigh 200g polypropylene and heat up to 200°C to obtain molten polypropylene, add 20g dicumyl peroxide, 40g maleic anhydride and 10mL acetone to the molten polypropylene, continue to keep warm and mix for 2 hours, and pour Extrude into a twin-screw machine to obtain modified polypropylene. Mix acrylamide solution with a mass fraction of 20%, dimethyl diallyl ammonium chloride and deionized water at a volume ratio of 3:1:2. ...
PUM
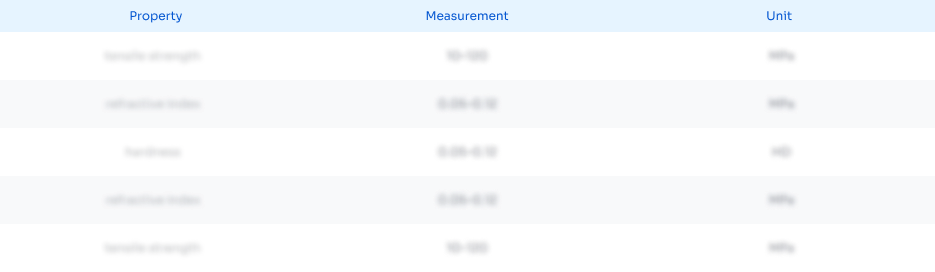
Abstract
Description
Claims
Application Information

- Generate Ideas
- Intellectual Property
- Life Sciences
- Materials
- Tech Scout
- Unparalleled Data Quality
- Higher Quality Content
- 60% Fewer Hallucinations
Browse by: Latest US Patents, China's latest patents, Technical Efficacy Thesaurus, Application Domain, Technology Topic, Popular Technical Reports.
© 2025 PatSnap. All rights reserved.Legal|Privacy policy|Modern Slavery Act Transparency Statement|Sitemap|About US| Contact US: help@patsnap.com