Reliability prediction method for macroscopic elastic performance of porous frame structure manufactured by 3D printing technology
A porous frame and 3D printing technology, applied in the field of level certification, can solve the problems of reliability increase, huge time and economic cost, etc., and achieve the effect of improving work efficiency, simple and feasible method, and avoiding the process of trial production and testing
- Summary
- Abstract
- Description
- Claims
- Application Information
AI Technical Summary
Problems solved by technology
Method used
Image
Examples
Embodiment Construction
[0039] according to figure 1 The flow of the forecasting method is shown, and the specific implementation process will be further described in detail below.
[0040] The first step, according to the actual application requirements, such as figure 2 Shown is the simplified design model. It is planned to use laser selective sintering technology to print this metal microstructure.
[0041] In the second step, for the design in the first step, according to the principle of establishing defect evaluation and quality certification, select three different printing service companies, use the same martensitic steel powder, have the same average particle size, and meet the particle size distribution Dispersion requirements. There are two communication printing directions, one is the horizontal direction (0°), and the other is the printing strategy at 45° to the horizontal direction (45°).
[0042]The third step is to observe and classify the 6 printed samples, and use the X-ray CT ...
PUM
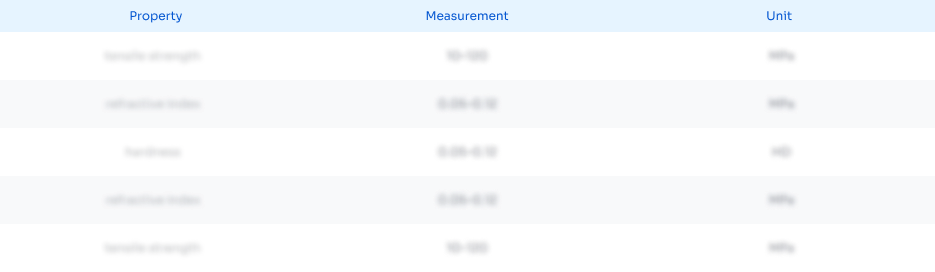
Abstract
Description
Claims
Application Information

- R&D Engineer
- R&D Manager
- IP Professional
- Industry Leading Data Capabilities
- Powerful AI technology
- Patent DNA Extraction
Browse by: Latest US Patents, China's latest patents, Technical Efficacy Thesaurus, Application Domain, Technology Topic, Popular Technical Reports.
© 2024 PatSnap. All rights reserved.Legal|Privacy policy|Modern Slavery Act Transparency Statement|Sitemap|About US| Contact US: help@patsnap.com