Upsetting force self-compensation stirring tool for aclinal frication stir welding and welding method
A technology of friction stir welding and stirring tools, applied in welding equipment, manufacturing tools, non-electric welding equipment, etc., can solve the problems of weak upsetting force, achieve less flash, eliminate hole defects, and have strong implementability
- Summary
- Abstract
- Description
- Claims
- Application Information
AI Technical Summary
Problems solved by technology
Method used
Image
Examples
Embodiment 1
[0034] combine figure 1 , 2 Describe the implementation mode, an upsetting force self-compensating stirring tool suitable for friction stir welding without inclination, including a clamping section 1, a cylindrical section 2 and a stirring pin 3, the three parts are integrated from top to bottom, and the material of the stirring tool is High speed tool steel. The clamping section 1 is a cylinder with a diameter of 20mm, and the side of the cylinder is milled with planes for fastening. Cylindrical section 2 is a cylinder with a diameter of 24mm. There are 3 circles of cooling grooves on the side. The outer ring of the shaft shoulder is flat and has 2 clockwise Archimedes spiral grooves. is 7°, the groove depth is 0.05~0.2mm, the outer ring of the shaft shoulder and the cylindrical section are provided with a chamfer of 0.5mm, the diameter of the inner ring of the shaft shoulder is 16mm and is concave, the concave angle is 7°, and the inner ring of the shaft shoulder The inne...
Embodiment 2
[0036] A welding method of upsetting force self-compensating stirring tool suitable for non-inclination friction stir welding, adopting the stirring tool as described in embodiment 1, clamping and fixing the 5mm thick aluminum alloy to be welded on the welding platform, using fastening The screw fixes the stirring tool on the friction stir welding equipment. The inclination angle of the main shaft of the equipment is set to 0°, the rotation direction of the main shaft is set to counterclockwise, and the speed of 800rpm is used to penetrate the material to be welded at a penetration speed of 3mm / min. 0.1mm, welding at a welding speed of 300mm / min, after the welding is completed, the stirring tool is pulled out, and the welding is completed.
PUM
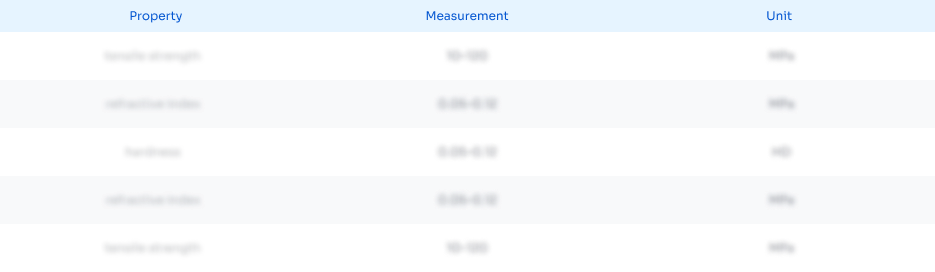
Abstract
Description
Claims
Application Information

- R&D
- Intellectual Property
- Life Sciences
- Materials
- Tech Scout
- Unparalleled Data Quality
- Higher Quality Content
- 60% Fewer Hallucinations
Browse by: Latest US Patents, China's latest patents, Technical Efficacy Thesaurus, Application Domain, Technology Topic, Popular Technical Reports.
© 2025 PatSnap. All rights reserved.Legal|Privacy policy|Modern Slavery Act Transparency Statement|Sitemap|About US| Contact US: help@patsnap.com