Flanged core material
A technology of flanging and core materials, which is applied to building components, insulation, construction, etc., can solve the problems of increasing labor intensity of construction personnel, excessive material waste, hidden safety hazards, etc., achieve light weight, reduce scrap rate, and improve safety Effect
- Summary
- Abstract
- Description
- Claims
- Application Information
AI Technical Summary
Problems solved by technology
Method used
Image
Examples
Embodiment 1
[0031] Such as figure 1 Shown: a flanging core material, including an upper panel 1, a lower panel 2, several core tubes 3 in the middle, and a brazing layer 4 between the core tube 3, the upper panel 1, and the lower panel 2, and the upper and lower sides of the core tube 3 Both ends are flanged, so that the outer diameter after flanging is greater than the diameter of the core tube 3; The sides 31 are closely arranged, and after the arrangement, the brazing layer 4 is formed on the flanging by brazing material.
[0032] The brazing layer 4 is punched and flanged, so that the core tube 3 is positioned on the flanging of the brazing layer 4 .
[0033] In this embodiment, the brazing material is copper brazing material, and the brazing layer 4 is provided with a hollow 5 at the non-core tube, and the hollow is formed into a triangle. The edge of the brazing layer 4 of the hollow 5 is strengthened by flanging, and the flanging is perpendicular to the plane of the brazing layer...
Embodiment 2
[0039] Such as figure 2 with image 3Shown: The difference from Example 1 is that a brazed sandwich composite panel includes an upper panel 1, a lower panel 2, several core tubes 3 in the middle, and a connection between the core tube 3 and the upper panel 1 and the lower panel 2. Brazing layer 4'; several core tubes 3 are arranged at intervals, and the distance between adjacent core tubes is 20mm. By arranging several core tubes at intervals, the number of core tubes can be saved, the cost can be reduced, and the brazing time can be shortened . The upper and lower ends of the core tube 3 are all flanged, and the flanges 31 of the core tube 3 and the upper panel 1, the lower panel 2 and between the flanges 31 of the core tube 3 and the flanges of other adjacent core tubes are brazed. Welded.
[0040] Specifically, the brazing layer 4' is punched and flanged, that is, the brazing material wraps the flanging 31 of the core tube 3 and extends into the core tube 3, so that the...
Embodiment 3
[0046] Such as Figure 4 Shown: the difference from Example 2 is that the brazing layer 4 is provided with a hollow 5 "at the non-core tube. Wherein, the specific structure of the hollow 5 " is: between the flanges 31 of adjacent core tubes 3 through brazing The welded connecting ribs 51 are connected into one body, that is, a radial structure is formed with the core tube 3 as the center, and a brazed rib 52 is arranged between the hollow structures between every three adjacent core tubes 3 to strengthen , that is, one of the connecting ribs 51 among the three adjacent core tubes 3 is provided with a reinforcing rib 52 between the flanges 31 of the core tube 3 opposite to it.
[0047] Other structures are with embodiment 1.
PUM
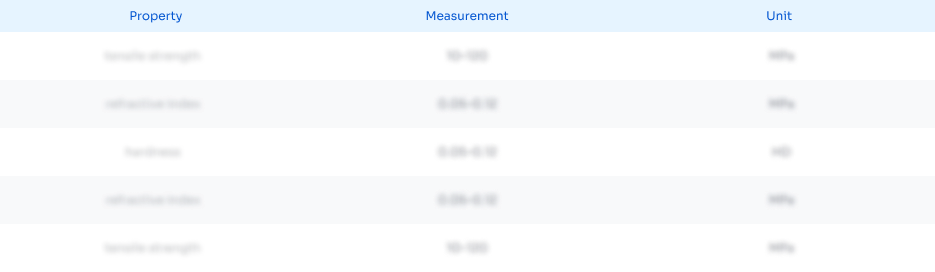
Abstract
Description
Claims
Application Information

- R&D
- Intellectual Property
- Life Sciences
- Materials
- Tech Scout
- Unparalleled Data Quality
- Higher Quality Content
- 60% Fewer Hallucinations
Browse by: Latest US Patents, China's latest patents, Technical Efficacy Thesaurus, Application Domain, Technology Topic, Popular Technical Reports.
© 2025 PatSnap. All rights reserved.Legal|Privacy policy|Modern Slavery Act Transparency Statement|Sitemap|About US| Contact US: help@patsnap.com