Device and method for tightening rear nuts of sealing disc of high-pressure rotor of aero-engine
An aero-engine, high-pressure rotor technology, applied in metal processing, metal processing equipment, manufacturing tools, etc., can solve the problems of inability to ensure the consistency of nut tightening, deformation of the device under load, long tightening transmission distance, etc., to reduce technical requirements and Labor intensity, guaranteed torque and angle accuracy, and the effect of reducing the tightening transmission distance
- Summary
- Abstract
- Description
- Claims
- Application Information
AI Technical Summary
Problems solved by technology
Method used
Image
Examples
Embodiment Construction
[0039] The specific embodiments of the present invention will be described in detail below in conjunction with the technical solutions and accompanying drawings.
[0040] like Figure 1-7 As shown, an aeroengine high-pressure rotor seal plate rear nut tightening device includes an indexing system 1 , a feed movement system 2 and a connecting rod tightening execution system 3 .
[0041] The indexing system 1 is fixedly installed on the rear shaft port of the high-pressure turbine rotor 6 through the flange 5 of the outer sleeve 4 .
[0042] The feed motion system 2 is located inside the indexing system 1, the middle sleeve 7 of the feed motion system 2 is connected with the outer sleeve 4 of the indexing system 1 through a bearing 8, and the indexing system 1 realizes the feed motion system 2 CNC rotation.
[0043] The link type tightening execution system 3 is located at the front end of the feed movement system 2, and the inner sleeve 9 of the link type tightening execution...
PUM
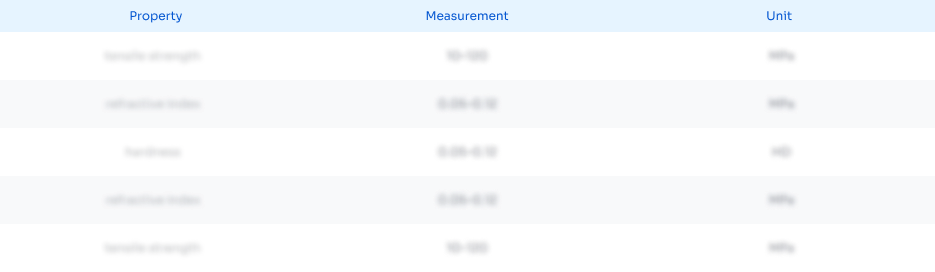
Abstract
Description
Claims
Application Information

- Generate Ideas
- Intellectual Property
- Life Sciences
- Materials
- Tech Scout
- Unparalleled Data Quality
- Higher Quality Content
- 60% Fewer Hallucinations
Browse by: Latest US Patents, China's latest patents, Technical Efficacy Thesaurus, Application Domain, Technology Topic, Popular Technical Reports.
© 2025 PatSnap. All rights reserved.Legal|Privacy policy|Modern Slavery Act Transparency Statement|Sitemap|About US| Contact US: help@patsnap.com