Drying and cooling system for production of cured powdery feed
A dry cooling, powdery technology, applied in cooling systems and drying fields, can solve the problems of troublesome box cleaning, low suspension speed, easy cross-contamination, etc., to ensure the cooling and drying effect, keep clean and hygienic, and avoid cross-contamination effects.
- Summary
- Abstract
- Description
- Claims
- Application Information
AI Technical Summary
Problems solved by technology
Method used
Image
Examples
Embodiment 1
[0045] Carry out drying and cooling when the conditioned powdery feed moisture of embodiment 1 is less than 18%
[0046] (1) Open the cooling air inlet, close the drying air inlet, start the cooling fan, all the cooling air enters from the air inlet on the side of the discharge hopper, and then start the cooler feeder to start feeding the cooler.
[0047] (2) The temperature of the mature powdery material coming out of the high-efficiency steam conditioner is 85-95°C, and the moisture content is 16%-18%. Lay flat on the multiple flaps that are equally arranged by the upper box discharge mechanism. When the powdery material is piled up to a height of about 300mm in the upper box, the upper material level device of the upper box sends out a signal, which makes the hydraulic cylinder or air cylinder push the crank connecting rod mechanism to move, and drives the flap to rotate around each axis, and the material will flow from each The gap between the flaps falls, enters the middle...
Embodiment 2
[0052] Carry out drying and cooling when the conditioned powdery feed moisture of embodiment 2 is greater than 18%
[0053] (1) Open the air inlet for cooling air and drying air, start the cooling fan, and feed steam into the steam heat exchanger of the drying air inlet pipeline, and the air used for drying will be heated when it passes through the steam heat exchanger, and the temperature will increase to 50-70 ℃, enter the cooler from the air inlet on the upper part of the middle box; the air used for cooling enters from the air inlet on the side of the discharge hopper, and then start the cooler feeder to start feeding the cooler.
[0054] (2), (3), (4) steps are the same as example 1
[0055] (5) The air used for cooling enters the lower box vertically from the gap of the overlapping part of the discharge flap at the bottom of the lower box, and then enters the middle box vertically from the gap of the overlapping part of the discharge flap at the bottom of the middle box....
PUM
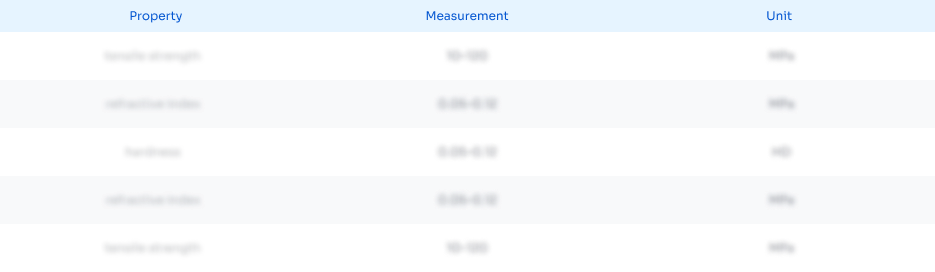
Abstract
Description
Claims
Application Information

- R&D
- Intellectual Property
- Life Sciences
- Materials
- Tech Scout
- Unparalleled Data Quality
- Higher Quality Content
- 60% Fewer Hallucinations
Browse by: Latest US Patents, China's latest patents, Technical Efficacy Thesaurus, Application Domain, Technology Topic, Popular Technical Reports.
© 2025 PatSnap. All rights reserved.Legal|Privacy policy|Modern Slavery Act Transparency Statement|Sitemap|About US| Contact US: help@patsnap.com