Reductive amination catalyst and preparation method
A catalyst and amination technology, which is applied in the direction of physical/chemical process catalysts, molecular sieve catalysts, amino compound preparation, etc. It can solve the problems of difficult continuous production of catalysts, low industrial application value, and short life, so as to improve nucleation and crystal grains Formation, improvement of activity, effect of enhancing activity
- Summary
- Abstract
- Description
- Claims
- Application Information
AI Technical Summary
Problems solved by technology
Method used
Image
Examples
Embodiment 1
[0030] Catalyst preparation:
[0031] At room temperature, add 74.0g nickel nitrate hexahydrate, 36.1g ferric nitrate nonahydrate, 2.6g rhodium chloride trihydrate into a mixed solvent of 60mL methanol and 240mL water, add 10mL ethanolamine, stir evenly, then add 30g titanium oxide and 49gY molecular sieve; the resulting mixture was left standing at room temperature for 24h, the solvent was removed under reduced pressure at 30°C, and dried at 120°C; shaped and calcined at 600°C for 4h to obtain the catalyst precursor; The volume space velocity is 1000h -1 hydrogen reduction for 3h to obtain the catalyst.
[0032] Catalytic Performance Evaluation:
[0033] Cool naturally to a temperature of 160°C, at a pressure of 8 MPa, the molar ratio of hydrogen to 1,2-propylenediamine is 2.5:1, and the molar ratio of raw material liquid ammonia to 1,2-propylene glycol is 15:1,1,2-propylene glycol Feed liquid space velocity is 1.56g / g cat The performance of the catalyst was evaluated und...
Embodiment 2
[0035] Catalyst preparation:
[0036] At room temperature, add 98.6g of nickel nitrate hexahydrate, 4.1g of ruthenium trichloride trihydrate and 13.6g of zinc nitrate hexahydrate into a mixed solvent of 70mL of ethanol and 210mL of water, add 10mL of ethanolamine, stir evenly, and then add 40g of fumed white Carbon black and 35g mordenite; the resulting mixture was left standing at room temperature for 12h, the solvent was removed under reduced pressure at 50°C, and dried at 120°C; shaped and calcined at 500°C for 4h to obtain the catalyst precursor; the catalyst precursor was heated at 450°C under normal pressure Under the condition, with the volumetric space velocity as 800h -1 The hydrogen reduction 4h, obtains described catalyst.
[0037] The catalytic performance evaluation conditions are the same as in Example 1, and the results are shown in Table 1.
Embodiment 3
[0039] Catalyst preparation:
[0040] At room temperature, add 123.3g of nickel nitrate hexahydrate and 5.1g of rhodium trichloride trihydrate into a mixed solvent of 60mL of n-propanol and 240mL of water, add 8mL of ethanolamine, stir well, then add 30g of fumed silica and 43g of β molecular sieve The resulting mixture was allowed to stand at room temperature for 16 hours, and the solvent was removed under reduced pressure at 50°C, and dried at 120°C; shaped and calcined at 450°C for 5 hours to obtain the catalyst precursor; Speed is 600h -1 The hydrogen reduction 4h, obtains described catalyst.
[0041] The catalytic performance evaluation conditions are the same as in Example 1, and the results are shown in Table 1.
PUM
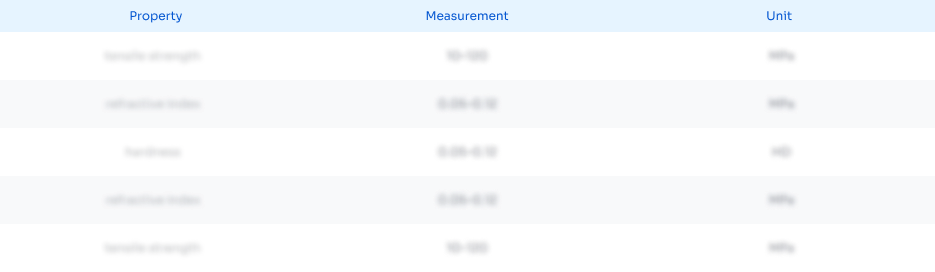
Abstract
Description
Claims
Application Information

- R&D
- Intellectual Property
- Life Sciences
- Materials
- Tech Scout
- Unparalleled Data Quality
- Higher Quality Content
- 60% Fewer Hallucinations
Browse by: Latest US Patents, China's latest patents, Technical Efficacy Thesaurus, Application Domain, Technology Topic, Popular Technical Reports.
© 2025 PatSnap. All rights reserved.Legal|Privacy policy|Modern Slavery Act Transparency Statement|Sitemap|About US| Contact US: help@patsnap.com