Technique of full width continuous pretreatment cleaning production of knitted fabrics
A process method and clean production technology, applied in the process field, can solve the problems of high production cost, long processing time, and high energy consumption, and achieve the effects of reducing material consumption, saving steam consumption, and reducing fiber loss
- Summary
- Abstract
- Description
- Claims
- Application Information
AI Technical Summary
Problems solved by technology
Method used
Image
Examples
Embodiment 1
[0029] Embodiment 1: A kind of open-width continuous pre-treatment cleaning production process method is carried out according to the following steps:
[0030] (1) Selection of degreasing and bleaching liquid additives and formula design:
[0031] Degreasing pretreatment is a very important first step to improve the water absorption and whiteness of the knitted gray fabric; through degreasing, the spinning oil and impurities on the gray fabric will be completely washed away; after prewashing, the fabric will be impregnated with scouring agent and Bleach, then steamed in a special steam box for knitwear, and then washed continuously, finally neutralized, rinsed, and discharged from the machine;
[0032] Preparation method of degreasing liquid: add 40% normal temperature water into the chemical tank, add degreasing liquid, stir and dissolve for 15 minutes, then add 30% water, continue stirring until uniform;
[0033] The preparation method of refining agent bleaching solution: ...
Embodiment 2
[0049] Embodiment 2: A kind of open-width continuous pre-treatment cleaning production process of knitted fabrics is carried out according to the following steps:
[0050] (1) Selection of degreasing and bleaching liquid additives and formula design:
[0051] Degreasing pretreatment is a very important first step to improve the water absorption and whiteness of the knitted gray fabric; through degreasing, the spinning oil and impurities on the gray fabric will be completely washed away; after prewashing, the fabric will be impregnated with scouring agent and Bleach, then steamed in a special steam box for knitwear, and then washed continuously, finally neutralized, rinsed, and discharged from the machine;
[0052] Preparation method of degreasing liquid: add 40% normal temperature water into the chemical tank, add degreasing liquid, stir and dissolve for 15 minutes, then add 30% water, continue stirring until uniform;
[0053] The preparation method of refining agent bleachin...
Embodiment 3
[0069] Embodiment 3: A kind of open-width continuous pre-treatment cleaning production process method is carried out according to the following steps:
[0070] (1) Selection of degreasing and bleaching liquid additives and formula design:
[0071] Degreasing pretreatment is a very important first step to improve the water absorption and whiteness of the knitted gray fabric; through degreasing, the spinning oil and impurities on the gray fabric will be completely washed away; after prewashing, the fabric will be impregnated with scouring agent and Bleach, then steamed in a special steam box for knitwear, and then washed continuously, finally neutralized, rinsed, and discharged from the machine;
[0072] Preparation method of degreasing liquid: add 40% normal temperature water into the chemical tank, add degreasing liquid, stir and dissolve for 15 minutes, then add 30% water, continue stirring until uniform;
[0073] The preparation method of refining agent bleaching solution: ...
PUM
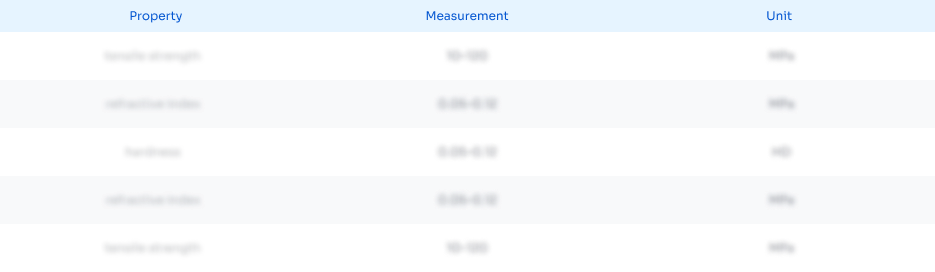
Abstract
Description
Claims
Application Information

- R&D Engineer
- R&D Manager
- IP Professional
- Industry Leading Data Capabilities
- Powerful AI technology
- Patent DNA Extraction
Browse by: Latest US Patents, China's latest patents, Technical Efficacy Thesaurus, Application Domain, Technology Topic, Popular Technical Reports.
© 2024 PatSnap. All rights reserved.Legal|Privacy policy|Modern Slavery Act Transparency Statement|Sitemap|About US| Contact US: help@patsnap.com