Novel cable coating composite material, and preparation method thereof
A composite material and cable technology, which is applied in the field of new cable coating composite materials and its preparation, can solve the problems of fire spread and high hazards, and achieve the goals of improving mechanical properties and heat resistance, improving flame retardancy, and reducing costs Effect
- Summary
- Abstract
- Description
- Claims
- Application Information
AI Technical Summary
Problems solved by technology
Method used
Examples
preparation example Construction
[0020] A preparation method of a novel cable coating composite material includes the following steps:
[0021] (1) Surface modification of anhydrous calcium sulfate: dissolve the coupling agent vinyl triethoxy silane in 250-290ml absolute ethanol, stir at 33-42°C for 3-5 hours, and filter for 6-7 with suction Then add the coupling agent vinyl triethoxy silane and calcium sulfate to absolute ethanol, and stir for 36-45 minutes, ultrasonic for 9-11 minutes, and then stir for 10-15 minutes; Water ethanol is suction filtered, washed 2-3 times, and then dried in a vacuum box at 45-55°C for 23-25 hours to obtain dry modified anhydrous calcium sulfate;
[0022] (2) Add polydimethylsiloxane and modified anhydrous calcium sulfate treated in step (1) into a high-speed mixer, stir at 30-35°C for 25-35min to obtain polydimethylsiloxane Mixture with modified anhydrous calcium sulfate;
[0023] (3) The mixture obtained in step (2) is solidified at a temperature of 100-170° C. for 40-60 min, an...
Embodiment 1
[0029] The weight ratio of raw materials in this embodiment: 65 parts of polydimethylsiloxane, 15 parts of calcium sulfate, and 35 parts of coupling agent vinyltriethoxysilane.
[0030] Preparation:
[0031] (1) Surface modification of anhydrous calcium sulfate: dissolve the coupling agent vinyl triethoxy silane in 250 ml of absolute ethanol, stir at 33°C for 3 hours, and filter 6 times with suction until the impurities are removed; The linking agent vinyl triethoxy silane and calcium sulfate are added to absolute ethanol and stirred for 40 minutes, ultrasonicated for 10 minutes, and then stirred for 15 minutes; then filtered with absolute ethanol, cleaned 3 times, and then placed in a vacuum box Dry at 50°C for 25 hours to obtain dry modified anhydrous calcium sulfate;
[0032] (2) Add polydimethylsiloxane and modified anhydrous calcium sulfate treated in step (1) into a high-speed mixer, stir at 33°C for 35min, to obtain polydimethylsiloxane and modified calcium sulfate A mixture...
Embodiment 2
[0036] The weight ratio of the raw materials in this embodiment: 55 parts of polydimethylsiloxane, 28 parts of calcium sulfate, and 45 parts of coupling agent vinyltriethoxysilane.
[0037] Preparation:
[0038] (1) Surface modification of anhydrous calcium sulfate: dissolve the coupling agent vinyl triethoxy silane in 250 ml of absolute ethanol, stir at 33°C for 3 hours, and filter 6 times with suction until the impurities are removed; The linking agent vinyl triethoxy silane and calcium sulfate are added to absolute ethanol and stirred for 40 minutes, ultrasonicated for 10 minutes, and then stirred for 15 minutes; then filtered with absolute ethanol, cleaned 3 times, and then placed in a vacuum box Dry at 50°C for 25 hours to obtain dry modified anhydrous calcium sulfate;
[0039] (2) Add polydimethylsiloxane and modified anhydrous calcium sulfate treated in step (1) into a high-speed mixer, stir at 33°C for 35min, to obtain polydimethylsiloxane and modified calcium sulfate A mix...
PUM
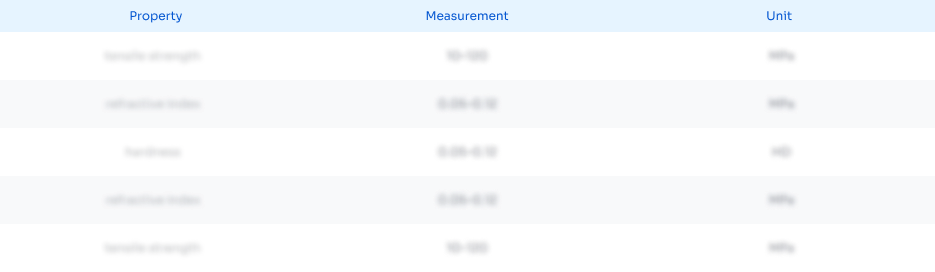
Abstract
Description
Claims
Application Information

- R&D Engineer
- R&D Manager
- IP Professional
- Industry Leading Data Capabilities
- Powerful AI technology
- Patent DNA Extraction
Browse by: Latest US Patents, China's latest patents, Technical Efficacy Thesaurus, Application Domain, Technology Topic, Popular Technical Reports.
© 2024 PatSnap. All rights reserved.Legal|Privacy policy|Modern Slavery Act Transparency Statement|Sitemap|About US| Contact US: help@patsnap.com