Assembling and welding process for box beam inserted and connected structure framework
A technology of plug-in structure and box girder, which is applied in the direction of welding/welding/cutting articles, manufacturing tools, welding equipment, etc. Beam assembly difficulties and other problems can be avoided to avoid positioning difficulties, shorten the frame manufacturing cycle, and improve welding quality
- Summary
- Abstract
- Description
- Claims
- Application Information
AI Technical Summary
Problems solved by technology
Method used
Image
Examples
Embodiment Construction
[0018] The present invention will be described in further detail below in conjunction with the accompanying drawings.
[0019] Such as Figure 1 to Figure 7 As shown, the assembly and welding process of the box girder plug-in structure framework of the present invention comprises the following steps:
[0020] Step 1. Welding of side beam 1 and semi-finished product of beam 2: complete the welding of all welds of side beam 1 according to the conventional welding sequence, and at the same time, weld the semi-finished product of beam 2 according to the following sequence:
[0021] Assemble the upper cover plate 2-1 of the crossbeam 2, the outer lateral vertical plate 2-2, the inner lateral vertical plate 2-3, the longitudinal vertical plate 2-4 and the rib plate 2-5, and complete the tack welding; then the Component A formed by tack welding is welded. When welding, first complete the welding of the interior of the cavity of component A and the upper cover plate 2-1 related trans...
PUM
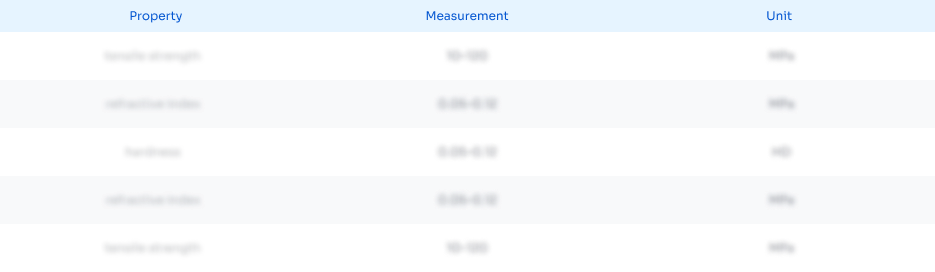
Abstract
Description
Claims
Application Information

- R&D
- Intellectual Property
- Life Sciences
- Materials
- Tech Scout
- Unparalleled Data Quality
- Higher Quality Content
- 60% Fewer Hallucinations
Browse by: Latest US Patents, China's latest patents, Technical Efficacy Thesaurus, Application Domain, Technology Topic, Popular Technical Reports.
© 2025 PatSnap. All rights reserved.Legal|Privacy policy|Modern Slavery Act Transparency Statement|Sitemap|About US| Contact US: help@patsnap.com