Rubber roller-vulcanized corrosion-resistant material and use method thereof
A technology of anti-corrosion materials and rubber rollers, which is applied in the direction of anti-corrosion coatings, fire-proof coatings, rubber derivative coatings, etc., can solve the problems of anti-corrosion materials that are difficult to clean, so as to avoid the appearance quality defects and dust pollution of the shaft head, protect the dead corners, Easy to remove clean effect
- Summary
- Abstract
- Description
- Claims
- Application Information
AI Technical Summary
Problems solved by technology
Method used
Image
Examples
Embodiment 1
[0040] A rubber roller vulcanization anticorrosion material and its preparation method and use method, the raw material components and mass percentage content of the rubber roller anticorrosion material are as shown in Table 1:
[0041] Table 1
[0042] Composition
weight percentage
silver paint
51%
Ethyl acetate or recovery solution
31%
18%
[0043] The raw material composition and mass percentage content of rubber roller vulcanized anticorrosion material, its preparation method and use method are as follows:
[0044] (1) At first weigh ethyl acetate, silver powder paint and powdery zinc oxide respectively, and place respectively stand-by;
[0045] (2) Add silver powder paint and ethyl acetate to the container at room temperature, and stir evenly until the ethyl acetate is completely dissolved;
[0046](3) Finally, add powdered zinc oxide and stir (stirring temperature is 50°C) until it is completely dissol...
Embodiment 2
[0055] A rubber roller vulcanization anticorrosion material and its preparation method and use method, the raw material components and mass percentage content of the rubber roller vulcanization anticorrosion material are as shown in Table 3:
[0056] table 3
[0057] Composition
weight percentage
silver paint
58%
Ethyl acetate or recovery solution
31%
powdered zinc oxide
11%
[0058] The source of each component of above-mentioned table is with embodiment 1.
[0059] The raw material composition and mass percentage content of rubber roller vulcanized anticorrosion material, its preparation method and use method are as follows:
[0060] (1) At first weigh ethyl acetate, silver powder paint and powdery zinc oxide respectively, and place respectively stand-by;
[0061] (2) Add silver powder paint and ethyl acetate to the container at room temperature, and stir evenly until the ethyl acetate is completely dissolved;
[0062] (3) F...
Embodiment 3
[0071] A rubber roller vulcanization anticorrosion material and its preparation method and use method, the raw material components and mass percentage content of the rubber roller vulcanization anticorrosion material are as shown in Table 5:
[0072] table 5
[0073] Composition
weight percentage
silver paint
54%
Ethyl acetate or recovery solution
35%
powdered zinc oxide
11%
[0074] The source of each component of above-mentioned table is with embodiment 1.
[0075] The raw material composition and mass percentage content of rubber roller vulcanized anticorrosion material, its preparation method and use method are as follows:
[0076] (1) At first weigh ethyl acetate, silver powder paint and powdery zinc oxide respectively, and place respectively stand-by;
[0077] (2) Add silver powder paint and ethyl acetate to the container at room temperature, and stir evenly until the ethyl acetate is completely dissolved;
[0078] (3) F...
PUM
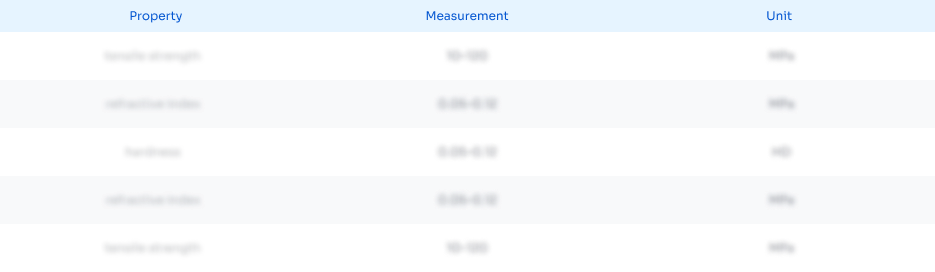
Abstract
Description
Claims
Application Information

- Generate Ideas
- Intellectual Property
- Life Sciences
- Materials
- Tech Scout
- Unparalleled Data Quality
- Higher Quality Content
- 60% Fewer Hallucinations
Browse by: Latest US Patents, China's latest patents, Technical Efficacy Thesaurus, Application Domain, Technology Topic, Popular Technical Reports.
© 2025 PatSnap. All rights reserved.Legal|Privacy policy|Modern Slavery Act Transparency Statement|Sitemap|About US| Contact US: help@patsnap.com