Comb row production process
A technology of production process and shape row, which is applied in the manufacture of contact box/base, assembly/disassembly of contacts, manufacturing of contacts, etc., can solve problems such as high dimensional accuracy requirements and comb-shaped rows that cannot be used normally, To achieve the effect of preventing oxidation, preventing movement difficulties, and avoiding the decrease of conductivity
- Summary
- Abstract
- Description
- Claims
- Application Information
AI Technical Summary
Problems solved by technology
Method used
Examples
Embodiment Construction
[0021] In order to understand the technical scheme of the present invention more intuitively and completely, the non-restrictive features are described as follows:
[0022] Comb row production technology is characterized in that comprising the following steps:
[0023] (1) Count punching, punching copper sheets of a certain width into two copper bars of the same size, for example, a 60mm wide copper bar can be punched into the same two pieces of workpieces;
[0024] (2) Bending, bending the copper bar;
[0025] (3) Grinding to remove the surface burrs of the copper bars;
[0026] (4) Tin plating, tin plating on the surface of the copper bar;
[0027] (5) Assemble, cut the insulating sheath, and accurately snap the copper bar into the insulating sheath.
[0028] The copper bar is copper, and the insulating sheath is PVC resin. Copper has good electrical conductivity and shape, and PVC resin has flame resistance, weather resistance, aging resistance, high impact temperature ...
PUM
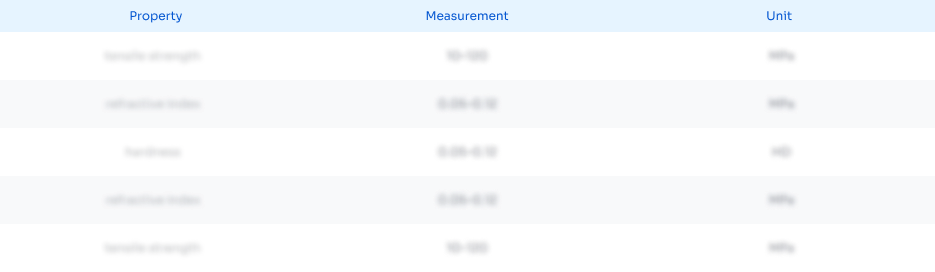
Abstract
Description
Claims
Application Information

- R&D
- Intellectual Property
- Life Sciences
- Materials
- Tech Scout
- Unparalleled Data Quality
- Higher Quality Content
- 60% Fewer Hallucinations
Browse by: Latest US Patents, China's latest patents, Technical Efficacy Thesaurus, Application Domain, Technology Topic, Popular Technical Reports.
© 2025 PatSnap. All rights reserved.Legal|Privacy policy|Modern Slavery Act Transparency Statement|Sitemap|About US| Contact US: help@patsnap.com