Grading and quality-dividing material distribution method in blast furnace
An internal classification and quality separation technology, applied in blast furnaces, blast furnace details, furnaces, etc., can solve problems such as airflow disorder, low gas utilization rate, small coke particle size, etc., to achieve flexible and simple operation, reduce fuel consumption, and control the process. Effect
- Summary
- Abstract
- Description
- Claims
- Application Information
AI Technical Summary
Problems solved by technology
Method used
Image
Examples
Embodiment approach
[0017] The batch weight of coke is 30 tons, and the distribution matrix is as follows:
[0018] C 1 2 3 4 5 6 7 12
[0019] 4 3 3 2 2 2 2 2
[0020] Among them, the 1st to 7th gears are a total of 18 rounds of ordinary coke (27 tons), and the 12th gear is 2 rounds of high-quality coke (3 tons).
[0021] A. Coke is screened or processed to obtain ordinary coke and high-quality coke, which are stored in different troughs;
[0022] B. Open the trough for storing high-quality coke, and send it into the material tank through belt 1-5 and belt 1-6. Rotate the baffle system 2-2 in the tank to fit the side wall of the tank, so that high-quality coke falls within the space surrounded by the baffle and the slope of the tank;
[0023] C. According to the smelting requirements, when the discharge of high-quality coke from the trough reaches the set value (3 tons), close the valve of the high-quality coke trough. Wait for 3 to 5 seconds, open the trough valve of ordinary coke, and fe...
PUM
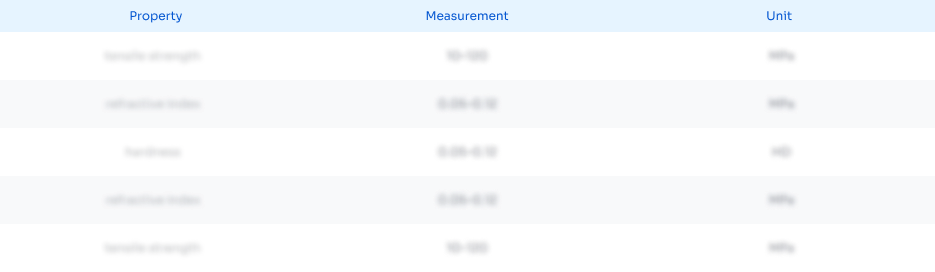
Abstract
Description
Claims
Application Information

- Generate Ideas
- Intellectual Property
- Life Sciences
- Materials
- Tech Scout
- Unparalleled Data Quality
- Higher Quality Content
- 60% Fewer Hallucinations
Browse by: Latest US Patents, China's latest patents, Technical Efficacy Thesaurus, Application Domain, Technology Topic, Popular Technical Reports.
© 2025 PatSnap. All rights reserved.Legal|Privacy policy|Modern Slavery Act Transparency Statement|Sitemap|About US| Contact US: help@patsnap.com