Gravity casting technique for crane wheel by hanging sand linings on graphite molds
A crane truck, gravity casting technology
- Summary
- Abstract
- Description
- Claims
- Application Information
AI Technical Summary
Problems solved by technology
Method used
Image
Examples
specific Embodiment 1
[0020] A gravity casting process of graphite type hanging sand lining for crane wheels, ready to be equipped with upper box graphite type 5 with upper box top plate 6, upper box cover box 7, upper bolt 8 and equipped with fixed square steel 14, lower box cover box 15 , the lower box graphite type 11 of the lower bolt 16, after baking to the set temperature, the required water glass sand upper box sand lining 4 and the lower box sand lining 9 are respectively shot by a sand shooting machine, and the CO of the set flow rate is blown into 2 Hardening and demoulding, the upper box sand lining 4 and the lower box sand lining 9 are respectively left on the upper box graphite type 5 and the lower box graphite type 11 through the sand hanging groove, and the rim graphite core 13 is placed on the rim of the lower box graphite type 11, and the lower box graphite type 11 is placed on the rim. The box sand lining 9 is placed with the process hole sand core 12 and the center core 10 made of...
specific Embodiment 2
[0021] This embodiment is further explained on the basis of specific embodiment 1. The corresponding wheel rim parts are in direct contact with the upper box graphite type 5, the lower box graphite type 11 and the rim graphite core 13 respectively, and the pouring riser 1 is arranged on the upper Box sand liner 4 corresponds to the top of the wheel hub.
specific Embodiment 3
[0022] This embodiment is further described on the basis of specific embodiment 1. The rim graphite core 13 can be replaced by a molding sand core made of water glass sand or resin sand.
PUM
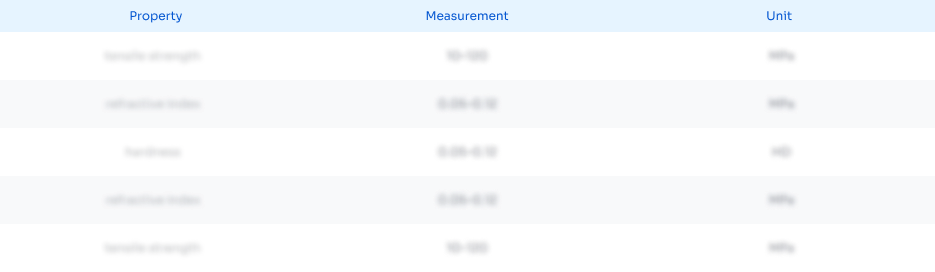
Abstract
Description
Claims
Application Information

- Generate Ideas
- Intellectual Property
- Life Sciences
- Materials
- Tech Scout
- Unparalleled Data Quality
- Higher Quality Content
- 60% Fewer Hallucinations
Browse by: Latest US Patents, China's latest patents, Technical Efficacy Thesaurus, Application Domain, Technology Topic, Popular Technical Reports.
© 2025 PatSnap. All rights reserved.Legal|Privacy policy|Modern Slavery Act Transparency Statement|Sitemap|About US| Contact US: help@patsnap.com