High wear-resistant iron based powder metallurgy internal spline, clutch cover and clutch
An iron-based powder metallurgy and internal spline technology, applied in the field of clutches, can solve the problems that engine power and output torque cannot be improved, reduce the performance and life of clutches, and the contact pressure of internal splines cannot be improved, and achieve friction pressure Improvement, improvement of wear resistance, performance and service life improvement effect
- Summary
- Abstract
- Description
- Claims
- Application Information
AI Technical Summary
Problems solved by technology
Method used
Examples
Embodiment 1
[0022] A high wear-resistant iron-based powder metallurgy internal spline, the composition of which is graphite 0.35%, copper 0.8%, nickel 0.35%, manganese 0.8%, chromium 1.3%, niobium 0.1%, titanium 0.1%, aluminum 0.1%, the rest is iron, and the sum of each component is 100%.
[0023] In this embodiment, the manufacturing method includes mixing, pressing, sintering, shaping, and processing, and the specific steps are as follows:
[0024] 1) Mixing: select graphite powder, copper powder, nickel powder, manganese powder, chromium powder, niobium powder, titanium powder, aluminum powder and iron powder according to the proportion and mix them evenly for use to obtain a powder composition;
[0025] 2) Compression: Put the powder composition mixed in step 1 into the blade embedded mold, press 6T / cm at room temperature 2 -7T / cm 2 The pressure of compressing the powder composition into a product blank;
[0026] 3) Sintering: Send the product blank obtained in step 2 into a sinter...
Embodiment 2
[0030] A high wear-resistant iron-based powder metallurgy internal spline, the composition of which is graphite 0.45%, copper 0.95%, nickel 0.45%, manganese 0.95%, chromium 1.45%, niobium 0.15%, titanium 0.15%, aluminum 0.15%, the rest is iron, and the sum of each component is 100%.
[0031] In this embodiment, the manufacturing method includes mixing, pressing, sintering, shaping, and processing, and the specific steps are as follows:
[0032] 1) Mixing: select graphite powder, copper powder, nickel powder, manganese powder, chromium powder, niobium powder, titanium powder, aluminum powder and iron powder according to the proportion and mix them evenly for use to obtain a powder composition;
[0033] 2) Compression: Put the powder composition mixed in step 1 into the blade embedded mold, press 6T / cm at room temperature 2 -7T / cm 2 The pressure of compressing the powder composition into a product blank;
[0034] 3) Sintering: Send the product blank obtained in step 2 into a ...
Embodiment 3
[0038] A high wear-resistant iron-based powder metallurgy internal spline, the composition of which is graphite 0.5%, copper 1.0%, nickel 0.5%, manganese 1.0%, chromium 1.5%, niobium 0.2%, titanium 0.2%, aluminum 0.2%, the rest is iron, and the sum of each component is 100%.
[0039] In this embodiment, the manufacturing method includes mixing, pressing, sintering, shaping, and processing, and the specific steps are as follows:
[0040] 1) Mixing: select graphite powder, copper powder, nickel powder, manganese powder, chromium powder, niobium powder, titanium powder, aluminum powder and iron powder according to the proportion and mix them evenly for use to obtain a powder composition;
[0041] 2) Compression: Put the powder composition mixed in step 1 into the blade embedded mold, press 6T / cm at room temperature 2 -7T / cm 2 The pressure of compressing the powder composition into a product blank;
[0042] 3) Sintering: Send the product blank obtained in step 2 into a sinterin...
PUM
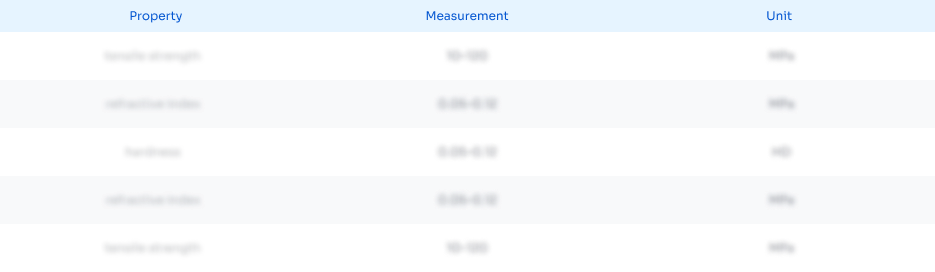
Abstract
Description
Claims
Application Information

- R&D Engineer
- R&D Manager
- IP Professional
- Industry Leading Data Capabilities
- Powerful AI technology
- Patent DNA Extraction
Browse by: Latest US Patents, China's latest patents, Technical Efficacy Thesaurus, Application Domain, Technology Topic, Popular Technical Reports.
© 2024 PatSnap. All rights reserved.Legal|Privacy policy|Modern Slavery Act Transparency Statement|Sitemap|About US| Contact US: help@patsnap.com