Tin dipping machine for processing wires
A technology of tin dipping machine and wire rod, applied in the field of tin dipping machine, can solve the problems of cumbersome structure, large space occupation, unfavorable production, etc.
- Summary
- Abstract
- Description
- Claims
- Application Information
AI Technical Summary
Problems solved by technology
Method used
Image
Examples
Embodiment Construction
[0047] refer to Figure 1 to Figure 20 , Figure 1 to Figure 20It is a structural schematic diagram of a specific embodiment of the present invention. As shown in the figure, a tin dipping machine for processing wire, a frame 1, a wire straightener 2, a wire feeding mechanism 3, a tool holder mechanism 4, a wire pulling mechanism 6, a tin Furnace mechanism 5, delivery mechanism 7.
[0048] The wire straightener 2 is arranged at the front end of the frame 1 to straighten the wire, as Figure 2 to Figure 5 As shown, the wire straightening device 2 includes: a wire feeding base plate 21, a straightening assembly 22, and a pre-feeding mechanism 23. It is arranged on the wire feeding substrate 21, which includes an upper straightening assembly and a lower straightening assembly capable of relative movement to straighten the wire; the pre-feeding mechanism 23 is located in front or behind the wire feeding direction of the straightening assembly 22, and the pre-feeding The wire me...
PUM
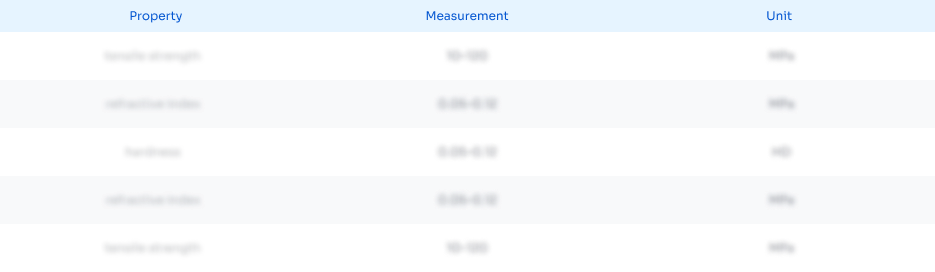
Abstract
Description
Claims
Application Information

- Generate Ideas
- Intellectual Property
- Life Sciences
- Materials
- Tech Scout
- Unparalleled Data Quality
- Higher Quality Content
- 60% Fewer Hallucinations
Browse by: Latest US Patents, China's latest patents, Technical Efficacy Thesaurus, Application Domain, Technology Topic, Popular Technical Reports.
© 2025 PatSnap. All rights reserved.Legal|Privacy policy|Modern Slavery Act Transparency Statement|Sitemap|About US| Contact US: help@patsnap.com