Connecting-rod underactuation bionics finger capable of self-adaptively grabbing
An underactuated and self-adaptive technology, applied in the field of intelligent robots, can solve the problems of high cost of lubrication and sealing of differential gear trains, difficult processing, difficult assembly, etc., and achieves simple structure, small size of mechanism structure and stable grasping Effect
- Summary
- Abstract
- Description
- Claims
- Application Information
AI Technical Summary
Problems solved by technology
Method used
Image
Examples
Embodiment Construction
[0036] as attached figure 1 As shown, the bionic finger of the present invention includes a first knuckle 1, a small connecting rod 2, a crank connecting rod 3, a trigger plate 4, a spring 5, a second knuckle 6, a first connecting shaft 7, a second connecting shaft 8, The third connecting shaft 9 , the fourth connecting shaft 10 , and the spring guide post 11 .
[0037] The bionic finger includes a first transmission chain and a second transmission chain. The first transmission chain includes a trigger plate 4 and a compression spring 5 connected together by adhesion, and the other end of the compression spring 5 is connected to the second phalanx 6 by adhesion. Together, the return movement of the trigger plate 4 is realized. The second transmission chain includes that the first knuckle 1 and the second knuckle 6 are hinged together by a rivet, and at the same time are hinged together with the small connecting rod 2 by a rivet, and the small connecting rod 2 and the crank co...
PUM
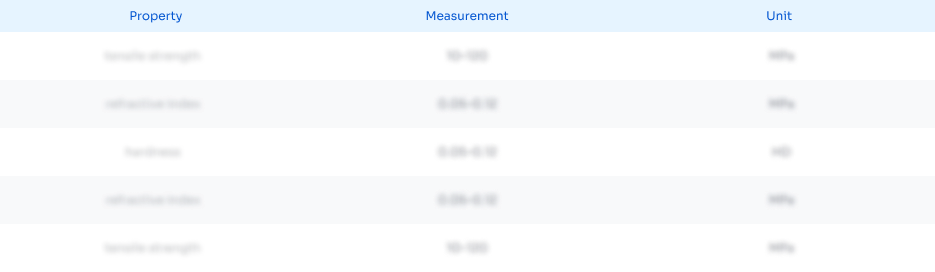
Abstract
Description
Claims
Application Information

- Generate Ideas
- Intellectual Property
- Life Sciences
- Materials
- Tech Scout
- Unparalleled Data Quality
- Higher Quality Content
- 60% Fewer Hallucinations
Browse by: Latest US Patents, China's latest patents, Technical Efficacy Thesaurus, Application Domain, Technology Topic, Popular Technical Reports.
© 2025 PatSnap. All rights reserved.Legal|Privacy policy|Modern Slavery Act Transparency Statement|Sitemap|About US| Contact US: help@patsnap.com