Low-frequency vibration isolation system and vibration reduction method
A vibration isolation system, low-frequency technology, applied in control/regulation system, mechanical vibration control, non-electric variable control, etc., can solve the problems of weakening low-frequency vibration isolation effect, large static deformation of the system, large bearing capacity, etc., and achieve high Performance Low-frequency vibration isolation effect, low initial frequency of vibration isolation, and small input energy
- Summary
- Abstract
- Description
- Claims
- Application Information
AI Technical Summary
Problems solved by technology
Method used
Image
Examples
Embodiment Construction
[0033] The present invention will be described in further detail below in conjunction with the accompanying drawings and specific implementation, with the purpose of helping those skilled in the art to have a more complete, accurate and in-depth understanding of the concept and technical solutions of the present invention, and to facilitate implementation.
[0034] Such as figure 1As shown, a low-frequency vibration isolation system of the present invention includes a quasi-zero stiffness module, a vibration signal monitoring module, a control module and an execution module, wherein the quasi-zero stiffness module is connected with the vibration signal monitoring module, the control module and the execution module in turn; The quasi-zero stiffness module includes a T-shaped load platform, a magnetic negative stiffness mechanism, a positive stiffness mechanical spring, and a support plate from top to bottom. Among them, the magnetic negative stiffness mechanism uses a double-rin...
PUM
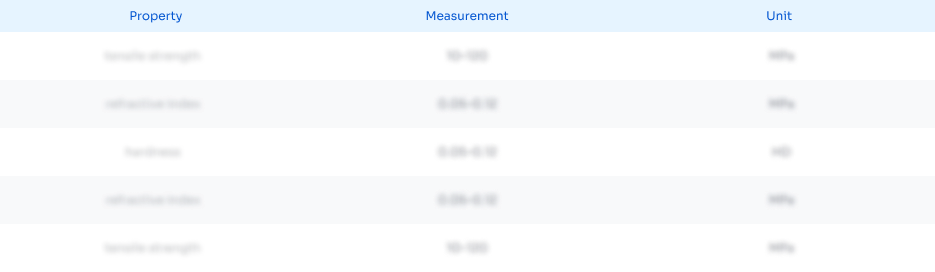
Abstract
Description
Claims
Application Information

- R&D
- Intellectual Property
- Life Sciences
- Materials
- Tech Scout
- Unparalleled Data Quality
- Higher Quality Content
- 60% Fewer Hallucinations
Browse by: Latest US Patents, China's latest patents, Technical Efficacy Thesaurus, Application Domain, Technology Topic, Popular Technical Reports.
© 2025 PatSnap. All rights reserved.Legal|Privacy policy|Modern Slavery Act Transparency Statement|Sitemap|About US| Contact US: help@patsnap.com