Method for extracting magnesium oxide from desulfurization wastewater produced from magnesium desulfurization
A desulfurization wastewater, magnesium desulfurization technology, applied in the direction of magnesium oxide, chemical instruments and methods, gaseous effluent wastewater treatment, etc., can solve the problems of reducing investment benefits, not using waste heat, etc., and achieve the effect of reducing operating costs and low costs
- Summary
- Abstract
- Description
- Claims
- Application Information
AI Technical Summary
Problems solved by technology
Method used
Examples
Embodiment 1
[0024] (1) Take 100mL of sintering desulfurization waste water in a round bottom flask, and heat it in a water bath at 45°C at a constant temperature, take 50mL of ammonia water in a constant pressure dropping funnel, slowly drop it into the round bottom flask for about 0.5h, and stir in time ;
[0025] (2) After the ammonia water is added dropwise, age for 1 hour, filter the formed magnesium hydroxide precipitate with a sandstone suction filter, and wash it with distilled water for 4 times to obtain solid magnesium hydroxide.
[0026] (3) The magnesium hydroxide solid was calcined in a muffle furnace at 700°C, evaporated to remove water, and the magnesium oxide solid was obtained, and the purity of the magnesium oxide was detected to be 86.75%, which met the requirements of a steel plant for recycling as a desulfurization absorbent, greatly The operation cost of magnesium desulfurization is reduced.
Embodiment 2
[0028] (1) Take 100mL of sintering desulfurization wastewater in a round bottom flask, and heat it in a water bath at 50°C at a constant temperature, take 75mL of ammonia water in a constant pressure dropping funnel, slowly drop it into the round bottom flask for about 0.5h, and stir in time ;
[0029] (2) After the ammonia water is added dropwise, age for 1 hour, filter the formed magnesium hydroxide precipitate with a sandstone suction filter, and wash it with distilled water for 5 times to obtain solid magnesium hydroxide.
[0030] (3) The magnesium hydroxide solid was calcined in a muffle furnace at 700°C, evaporated to remove water, and the magnesium oxide solid was obtained, and the purity of the magnesium oxide was detected to be 88.81%, which meets the requirements of a steel plant for recycling as a desulfurization absorbent, greatly The operation cost of magnesium desulfurization is reduced.
PUM
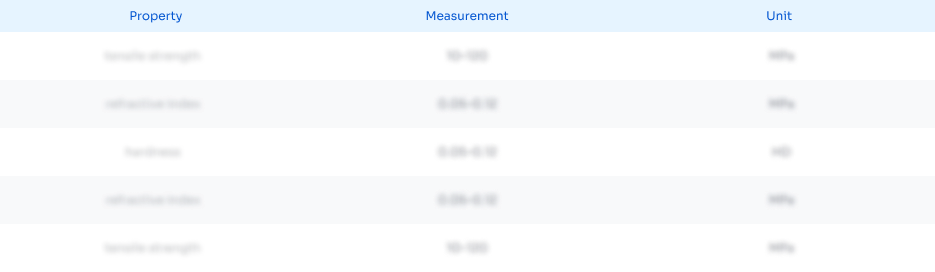
Abstract
Description
Claims
Application Information

- R&D Engineer
- R&D Manager
- IP Professional
- Industry Leading Data Capabilities
- Powerful AI technology
- Patent DNA Extraction
Browse by: Latest US Patents, China's latest patents, Technical Efficacy Thesaurus, Application Domain, Technology Topic, Popular Technical Reports.
© 2024 PatSnap. All rights reserved.Legal|Privacy policy|Modern Slavery Act Transparency Statement|Sitemap|About US| Contact US: help@patsnap.com