Full mold casting method for large grinder bed
A technology of full mold casting and bed, which is applied in the field of casting processing, can solve the problems of casting surface area carbon, slag holes and pores, easy deformation of shape, etc., and achieve the effects of easy operation, sufficient gasification, and high yield
- Summary
- Abstract
- Description
- Claims
- Application Information
AI Technical Summary
Problems solved by technology
Method used
Image
Examples
Embodiment Construction
[0028] See attached picture:
[0029] A full mold casting method for a large grinding machine bed, comprising the following steps:
[0030] 1) Make a white mold, use foam sand to form a foam model with the same size and shape as the grinder bed, choose expandable methyl methacrylate and styrene copolymer resin particles, and inject 1.2~1.4kg of steam at a time Bubble machine processing;
[0031] 2) White mold coating: The surface of the white mold is coated with three layers. The first layer is painted with zircon powder alcohol-based paint, and then two layers are coated with graphitic alcohol-based paint. The total thickness of the three layers is controlled at 1.0~1.45mm After painting, let it dry for 1.5~2 hours;
[0032] 4) White mold modeling: First, fill the inner cavity of the model with a white mold of the same material, fill the dead corners that are easy to stick to sand with a chrome ore mixed resin curing agent, and turn over the filling material in the second p...
PUM
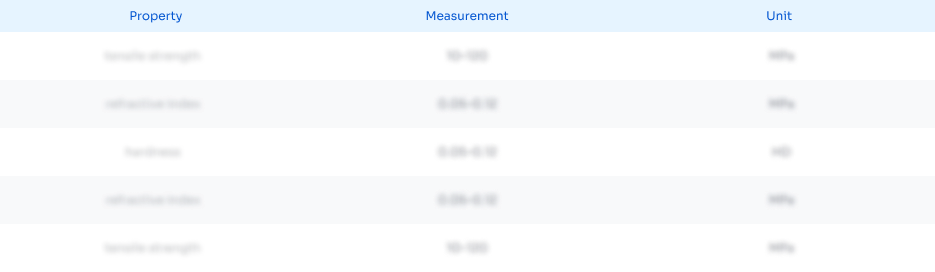
Abstract
Description
Claims
Application Information

- R&D
- Intellectual Property
- Life Sciences
- Materials
- Tech Scout
- Unparalleled Data Quality
- Higher Quality Content
- 60% Fewer Hallucinations
Browse by: Latest US Patents, China's latest patents, Technical Efficacy Thesaurus, Application Domain, Technology Topic, Popular Technical Reports.
© 2025 PatSnap. All rights reserved.Legal|Privacy policy|Modern Slavery Act Transparency Statement|Sitemap|About US| Contact US: help@patsnap.com