A transfer plate pretreatment device and transfer printing equipment
A technology of pretreatment device and transfer plate, which is applied in the direction of surface pretreatment, device for coating liquid on the surface, transportation and packaging, etc. It can solve the problems of chemical reagent harm, long soaking time period, etc., and improve the utilization rate. , Improve the transfer effect, shorten the time effect
- Summary
- Abstract
- Description
- Claims
- Application Information
AI Technical Summary
Problems solved by technology
Method used
Image
Examples
Embodiment 1
[0041] This embodiment provides a transfer plate pretreatment device, such as figure 1 As shown, it includes a driving roller 1 and a pressure roller 2 that are arranged correspondingly. The driving roller 1 includes a heating layer for heating the transfer plate 3 spread thereon, and the pressure roller 2 is used for heating the transfer plate 3 spread on it. The transfer plate 3 on the driving roller 1 is squeezed to improve the wettability of the transfer plate 3 .
[0042] Wherein, the driving roller 1 is a cylindrical roller, and the pressing roller 2 is also a cylindrical roller. By laying the transfer printing plate 3 on the cylindrical surface of the driving roller 1, and heating and pressing it, the slope angle of the mesh layer of the transfer printing plate 3 can be increased microscopically, thereby reducing macroscopically. The contact angle between the small transfer printing plate 3 and the transfer printing plate 3 (such as making the contact angle of the tran...
Embodiment 2
[0061] This embodiment provides a transfer printing device, such as Figure 5 As shown, it includes the transfer plate pretreatment device in Example 1; it also includes a plate hanging mechanism 6 and a plate ketone 7, and the plate hanging mechanism 6 is arranged between the transfer plate pretreatment device and the plate ketone 7 for transferring The transfer printing plate 3 processed by the printing plate pretreatment device is hung on the plate ketone 7 .
[0062] By adopting the transfer plate pretreatment device in Example 1, before the transfer plate 3 is hung on the plate ketone 7, the wettability of the transfer plate 3 can be automatically improved to increase its wettability, so that the The transfer printing equipment can automatically improve the wettability of the transfer printing plate 3 before hanging the plate, thereby improving the printing efficiency and utilization rate of the transfer printing equipment.
[0063] Among them, the setting of the plate h...
PUM
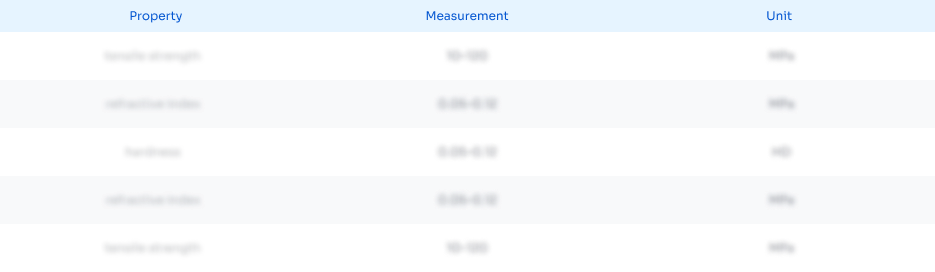
Abstract
Description
Claims
Application Information

- R&D Engineer
- R&D Manager
- IP Professional
- Industry Leading Data Capabilities
- Powerful AI technology
- Patent DNA Extraction
Browse by: Latest US Patents, China's latest patents, Technical Efficacy Thesaurus, Application Domain, Technology Topic, Popular Technical Reports.
© 2024 PatSnap. All rights reserved.Legal|Privacy policy|Modern Slavery Act Transparency Statement|Sitemap|About US| Contact US: help@patsnap.com