Cast-in-situ skeleton, preparation method and structural wall prepared from skeleton
A cast-in-place and skeleton technology, applied to walls, building components, building structures, etc., can solve the problems of increased construction procedures, complicated materials, affecting thermal insulation effect and service life, etc.
- Summary
- Abstract
- Description
- Claims
- Application Information
AI Technical Summary
Problems solved by technology
Method used
Image
Examples
Embodiment Construction
[0085] The structure and application principle of the cast-in-place framework, the preparation method of the cast-in-place framework and the structural wall prepared by using the cast-in-place framework of the present invention will be further described in detail below in conjunction with the accompanying drawings and specific embodiments.
[0086] In order to express more clearly, the inner side and the outer side expressed in the text are relative to the entire cast-in-place framework, that is, the side of the cast-in-place framework with the first membrane shell is defined as the outer side, and the side with the second membrane shell is defined as the outer side. Side is defined as medial.
[0087] Such as figure 1 , figure 2 and image 3 As shown, the cast-in-place framework of the present invention includes the first membrane shell 1 located on the outermost side, and the inner surface of the first membrane shell 1 is provided with a keel 2 containing at least two paral...
PUM
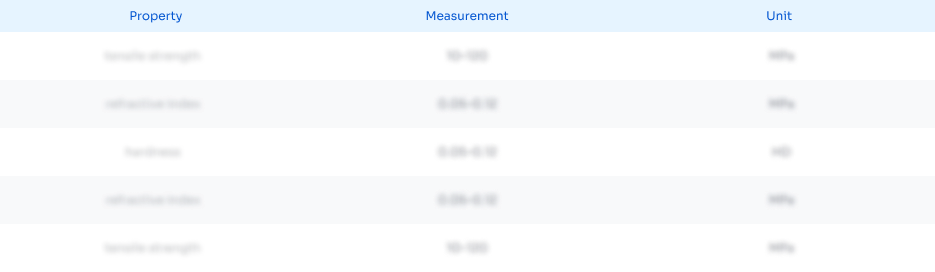
Abstract
Description
Claims
Application Information

- R&D Engineer
- R&D Manager
- IP Professional
- Industry Leading Data Capabilities
- Powerful AI technology
- Patent DNA Extraction
Browse by: Latest US Patents, China's latest patents, Technical Efficacy Thesaurus, Application Domain, Technology Topic, Popular Technical Reports.
© 2024 PatSnap. All rights reserved.Legal|Privacy policy|Modern Slavery Act Transparency Statement|Sitemap|About US| Contact US: help@patsnap.com