Stainless steel slag granulating device and method
A stainless steel slag and granulation technology, which is applied in the treatment of molten stainless steel slag and the field of stainless steel slag granulation equipment, can solve the problems of increasing the processing cost per ton of slag, affecting the environment of the work site, and high production and operation costs, so as to alleviate the long cooling period, Significant environmental benefits and economic benefits, the effect of less equipment construction
- Summary
- Abstract
- Description
- Claims
- Application Information
AI Technical Summary
Problems solved by technology
Method used
Image
Examples
Embodiment 1
[0083] Such as figure 1 As shown, this embodiment provides a stainless steel slag granulation device, including a slag tank mechanism, a casting mechanism and a quenching mechanism 8 connected in sequence; the slag tank mechanism includes a slag tank 1 with a heating function and a slag tank tipping device 2; The casting mechanism includes an ingot device 3, a dust removal device 4, a cooling device 5 and a steam collection device 6, the dust removal device 4 is arranged above the ingot device 3, the steam collection device 6 is located between the dust removal device 4 and the ingot device 3, and cooling The device 5 is located below the steam collecting device 6; the inlet end and the outlet end of the ingot device 3 are respectively connected with the slag tank mechanism and the quenching mechanism 8.
[0084] Wherein, the slag tank 1 with heating function includes a slag tank and an electric heating device placed in the slag tank. The slag tank tipping device 2 includes a...
Embodiment 2
[0089] The composition of typical stainless steel slag includes: Fe 0.32%, SiO 2 2.88%, CaO 62.79%, MgO4.52%, Al 2 o 3 1.02%, MnO 0.24%, S 0.66% and Cr 2 o 3 0.58%.
[0090] The temperature of stainless steel slag is generally about 1600°C. When slag is discharged, it is loaded into a slag tank with heating function, and transported by a slag tank truck to an environmental protection granulation workshop for granulation treatment of stainless steel slag. The stainless steel slag granulation method includes the following steps:
[0091] (a) Liquid slag heat preservation: use a slag tank with a heating function to control the temperature of the stainless steel slag to 1300°C;
[0092] (b) The casting mechanism starts: start the ingot device and the dust removal device, and wait for casting;
[0093](c) Casting: adjust the tipping angle of the continuous slag tank tipping device, so that the liquid stainless steel slag is evenly poured into the ingot device, and cast into...
Embodiment 3
[0098] A stainless steel slag granulation method, comprising the following steps:
[0099] (a) Liquid slag insulation: use a slag tank with a heating function to control the temperature of the stainless steel slag to 1600°C;
[0100] (b) The casting mechanism starts: start the ingot device and the dust removal device, and wait for casting;
[0101] (c) Casting: adjust the tipping angle of the continuous slag tank tipping device, so that the liquid stainless steel slag is evenly poured into the ingot device, and cast into a block-shaped slag block of 100mm×100mm×40mm;
[0102] (d) Water spray cooling: start the cooling device, spray water to cool the blocky slag, and cool it to 700°C;
[0103] (e) block unloading: unload the cooled blocky slag from the discharge device at the end of the ingot device into the quenching water pool for quenching, and the quenching time is 4h;
[0104] (f) Slag discharge: The slag particles in the quenching water pool are cleared out through the ...
PUM
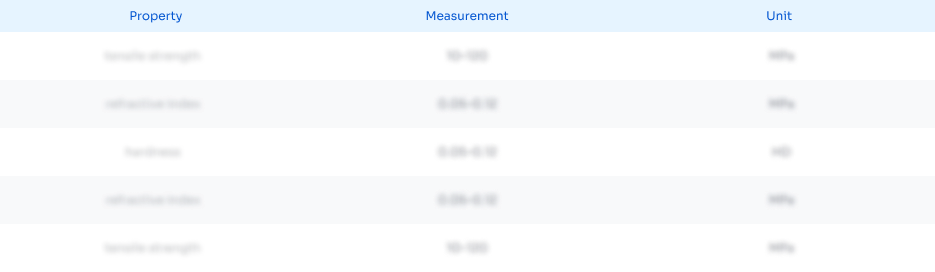
Abstract
Description
Claims
Application Information

- R&D Engineer
- R&D Manager
- IP Professional
- Industry Leading Data Capabilities
- Powerful AI technology
- Patent DNA Extraction
Browse by: Latest US Patents, China's latest patents, Technical Efficacy Thesaurus, Application Domain, Technology Topic, Popular Technical Reports.
© 2024 PatSnap. All rights reserved.Legal|Privacy policy|Modern Slavery Act Transparency Statement|Sitemap|About US| Contact US: help@patsnap.com