Epoxy pouring process for liquid tank saddle of liquefied gas transport ship
A technology of epoxy pouring and transport ship, which is applied in the field of liquid tank entering cargo hold process, can solve the problems of improper stirring method, not in a suitable range, ignoring preheating and ambient temperature, etc., and achieve the effect of preventing confusion
- Summary
- Abstract
- Description
- Claims
- Application Information
AI Technical Summary
Problems solved by technology
Method used
Examples
Embodiment Construction
[0023] The invention discloses an epoxy pouring process for a liquid tank saddle of a liquefied gas transport ship.
[0024] The specific steps of the injection process are as follows:
[0025] (1) Preparation: The number of participating operators and smearing workers shall be organized and arranged in advance; sufficient lighting, tools, and power sockets shall be provided in the cargo hold; EPOCAST36-P epoxy resin with two-component paste material shall be prepared, and the main agent shall be brown in color. The thick paste cement, the curing agent is light yellow yellow cement (the epoxy resin should be stored in a dry place and away from direct sunlight. The valid period of use is 12 months after leaving the factory, and the best use time is within 10 months after leaving the factory); The construction team prepared thin pine wood strips of 30mm×15mm and used them when the epoxy resin was sagging. The length of the pine wood strips was divided on site according to the wi...
PUM
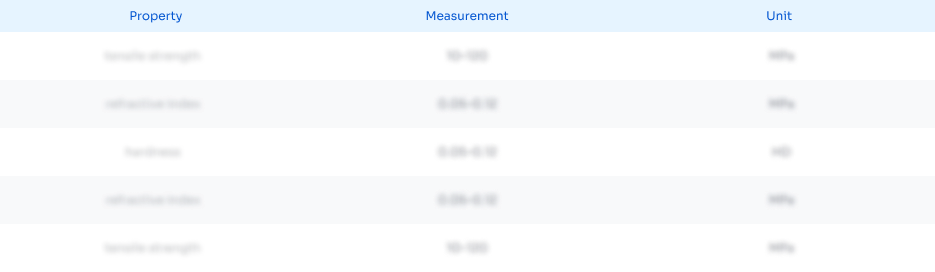
Abstract
Description
Claims
Application Information

- R&D
- Intellectual Property
- Life Sciences
- Materials
- Tech Scout
- Unparalleled Data Quality
- Higher Quality Content
- 60% Fewer Hallucinations
Browse by: Latest US Patents, China's latest patents, Technical Efficacy Thesaurus, Application Domain, Technology Topic, Popular Technical Reports.
© 2025 PatSnap. All rights reserved.Legal|Privacy policy|Modern Slavery Act Transparency Statement|Sitemap|About US| Contact US: help@patsnap.com