Monolithic catalyst and preparation and application thereof
A monolithic catalyst, monolithic catalyst technology, applied in the field of coal chemical industry, can solve the problems of low reaction activity, low operating space velocity, high energy consumption and material consumption, etc.
- Summary
- Abstract
- Description
- Claims
- Application Information
AI Technical Summary
Problems solved by technology
Method used
Image
Examples
Embodiment 1
[0055] a) Coating preparation: 10g of hydroxyapatite Ca 5 (PO 4 ) 3 (OH) and 60 g of deionized water were mixed in a 100 ml ball mill tank, the speed of the ball mill was adjusted to 500 r / min, and the catalyst coating carrier slurry was obtained after ball milling for 6 hours. Select a monolithic catalyst carrier with a pore size of 400 holes / square inch, dip the coating carrier slurry for 3 minutes, then use compressed air to remove excess liquid slurry in the channel of the monolithic catalyst carrier, and repeat the above coating after drying. The coating step was carried out 3 times, and the weight of the coated catalyst promoter was weighed to be 20% of the overall catalyst carrier, and it was placed in a muffle furnace for calcination at 400° C. for 2 h.
[0056] b) Take 0.03g Nd(NO 3 ) 3 ﹒ 6H 2 O dissolved in 5ml of water to form Nd(NO 3 ) 3 solution, impregnating the above-mentioned additive-free carrier in the solution for 2 hours, and then drying at 80° C. f...
Embodiment 2
[0062] a) Coating preparation: 10g of hydroxyapatite Ca 5 (PO 4 ) 3 (OH) and 60 g of deionized water were mixed in a 100 ml ball mill tank, the speed of the ball mill was adjusted to 500 r / min, and the catalyst coating carrier slurry was obtained after ball milling for 6 hours. Select a monolithic catalyst carrier with a pore size of 400 holes / square inch, dip the coating carrier slurry for 3 minutes, then use compressed air to remove excess liquid slurry in the channel of the monolithic catalyst carrier, and repeat the above coating after drying. The coating step was carried out 3 times, and the weight of the coated catalyst promoter was weighed to be 20% of the overall catalyst carrier, and it was placed in a muffle furnace for calcination at 400° C. for 2 h.
[0063] b) Take 0.03g Nd(NO 3 ) 3 ﹒ 6H 2 O dissolved in 5ml of water to form Nd(NO 3 ) 3 solution, impregnating the above-mentioned additive-free carrier in the solution for 2 hours, and then drying at 80° C. f...
Embodiment 3
[0068] a) Coating preparation: 10 g of Beta molecular sieve and 60 g of deionized water were mixed, ultrasonically treated for 30 min and then stirred for 2 h to obtain catalyst coating carrier slurry. Select an integral catalyst carrier with a channel mesh number of 600 holes / square inch, dip the coating carrier slurry for 3 minutes, then use compressed air to remove excess liquid slurry in the channel of the integral catalyst carrier, and repeat the above coating after drying. The coating step was carried out 3 times, and the weight of the coated catalyst promoter was weighed to be 20% of the overall catalyst carrier, and it was placed in a muffle furnace for calcination at 400° C. for 2 h.
[0069] b) take 1.92g (NH 4 ) 2 HPO 4 Dissolve in 10ml of water to form a solution, impregnate the additive-free carrier prepared in the above steps in this solution for 2 hours, then dry it at 80°C for 12 hours, place it in a muffle furnace and bake it at 400°C for 2 hours to obtain a...
PUM
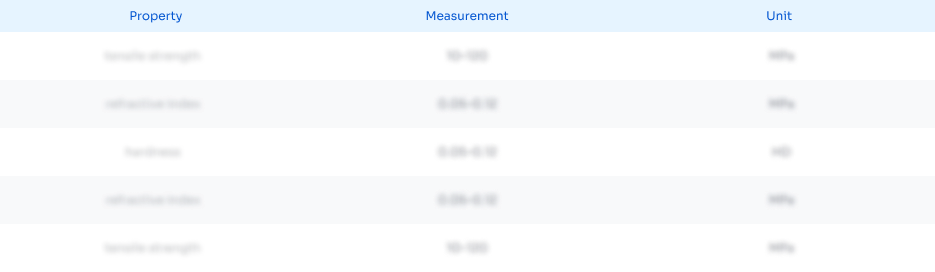
Abstract
Description
Claims
Application Information

- R&D
- Intellectual Property
- Life Sciences
- Materials
- Tech Scout
- Unparalleled Data Quality
- Higher Quality Content
- 60% Fewer Hallucinations
Browse by: Latest US Patents, China's latest patents, Technical Efficacy Thesaurus, Application Domain, Technology Topic, Popular Technical Reports.
© 2025 PatSnap. All rights reserved.Legal|Privacy policy|Modern Slavery Act Transparency Statement|Sitemap|About US| Contact US: help@patsnap.com