Jet printing process of fur fabric
A technology for fabrics and furs, applied in the field of spraying process of fur fabrics, can solve the problems of violation of environmental protection regulations and sustainable development requirements, stiff hand feeling, water pollution sources, etc., achieve strong randomness in color matching, avoid water pollution, avoid fading effect
- Summary
- Abstract
- Description
- Claims
- Application Information
AI Technical Summary
Problems solved by technology
Method used
Examples
Embodiment 1
[0031] Example 1: A flower spraying process for a light gray sheepskin fur fabric, choose a light gray sheepskin cut piece, and need to print a peony picture on the cut piece, the pattern size is 38cm×42cm:
[0032] Design pattern: Design the pattern as a vector diagram and produce a film;
[0033] Spray printing plate: select 45×70cm screen printing screen frame according to the design specifications, stretch the screen frame with 30-mesh mesh cloth and print the plate;
[0034] Seasoning: Prepare the color spray agent, and use red, yellow, and green leather dyes to make multiple color spray agents of different shades according to the following mass ratios:
[0035] Leather dye: diluent: 80°C hot water: color fixing agent: formic acid: 1°C tap water
[0036] 70g:25g:300g:25g:25g:200g
[0037] Position the spray plate on the piece to be sprayed according to the required position, and make it no longer shift;
[0038] Spray the yellow color spray evenly on the stamens of the...
Embodiment 2
[0042] Embodiment 2: A kind of flower spraying technique of light snow cyan fur integrated (suede) fur fabric, selects light snow cyan fur integrated (suede) cut piece, needs to print a butterfly pattern on the cut piece, pattern specification is 15× 20cm;
[0043] Design pattern: Design the pattern as a vector diagram and produce a film;
[0044] Spray printing plate: according to the design specifications, choose 55×70cm, 30×50cm screen printing frame, stretch the frame with 30 mesh cloth and print the plate;
[0045] Seasoning: Prepare color spray agents, and use black, red, yellow, and blue leather dyes to make multiple monochrome color spray agents in the following proportions:
[0046] Leather dye: diluent: 90°C hot water: color fixing agent: formic acid: 35°C purified water
[0047] 90g:35g:300g:45g:40g:200g
[0048] Position the spray plate on the cut piece according to the required position, and make it no longer shift;
[0049] Spray the black toner more and even...
Embodiment 3
[0054] Example 3: A flower spraying process of a pink fur fabric. When choosing a pink fur fabric, it is necessary to print an abstract picture of a zebra on the cut piece. The size of the pattern is 38cm×50cm. Circle-shaped strip pattern, the overall height of the pattern is 18cm;
[0055] Design pattern: Design the pattern as a vector diagram and produce a film;
[0056] Spray printing plate: according to the design specifications, select 55×70cm, 30×80cm screen printing frame, stretch the frame with 50 mesh cloth and print the plate;
[0057] Seasoning: deploying color spray agent, black monochrome color spray agent:
[0058] Leather dye: diluent: 100℃ hot water: fixing agent: formic acid: 25℃ well water
[0059] 80g:30g:300g:35g:40g:200g
[0060] Position the spray pattern on the piece to be sprayed according to the required position, and make it no longer shift;
[0061] Spray the black color spray evenly on the back pattern;
[0062] Use a steam steamer to steam the...
PUM
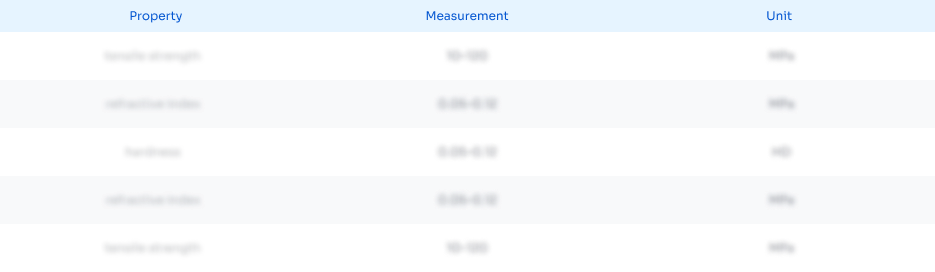
Abstract
Description
Claims
Application Information

- R&D
- Intellectual Property
- Life Sciences
- Materials
- Tech Scout
- Unparalleled Data Quality
- Higher Quality Content
- 60% Fewer Hallucinations
Browse by: Latest US Patents, China's latest patents, Technical Efficacy Thesaurus, Application Domain, Technology Topic, Popular Technical Reports.
© 2025 PatSnap. All rights reserved.Legal|Privacy policy|Modern Slavery Act Transparency Statement|Sitemap|About US| Contact US: help@patsnap.com