Aluminum alloy anode oxidation technology
An anodic oxidation and aluminum alloy technology, applied in the field of metal surface treatment, can solve problems such as difficulties, achieve the effects of increasing production efficiency, high hardness, and enhancing customer experience value
- Summary
- Abstract
- Description
- Claims
- Application Information
AI Technical Summary
Problems solved by technology
Method used
Image
Examples
Embodiment 1
[0023] An aluminum alloy anodizing process, comprising the steps of:
[0024] A. Degreasing: immerse the aluminum alloy profile in 8% sulfuric acid solution for 12 minutes and then take it out. The immersion temperature is 25°C;
[0025] B. Alkali cleaning: immerse the degreased aluminum alloy profile in 1.5mol / L sodium hydroxide lotion for 5 minutes, and the immersion temperature is 25°C;
[0026] C. Water washing: rinse the aluminum alloy profiles after alkali washing with water;
[0027] D. Anodizing: Place the washed aluminum alloy profile in an electrolytic cell with a concentration of 10% sulfuric acid solution for electrolysis. The electrolysis temperature is 30°C. The aluminum alloy profile is used as the anode and the lead plate is used as the cathode. The electrolysis method It is a method of DC-AC superimposition, so that an oxide film is formed on the surface of aluminum alloy profiles after anodic oxidation. The specific process of DC-AC superposition electrolysi...
Embodiment 2
[0033] The difference between embodiment 2 and embodiment 1 is that in step A, the concentration of sulfuric acid solution is 10%, the immersion time is 10min and then taken out, and the immersion temperature is 30°C.
Embodiment 3
[0035] The difference between Example 3 and Example 1 is that in step B, the degreased aluminum alloy profile is immersed in 2 mol / L sodium hydroxide washing solution for 3 minutes, and the immersion temperature is 30°C.
PUM
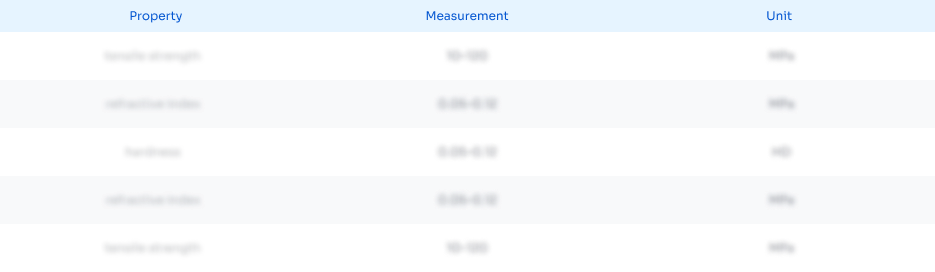
Abstract
Description
Claims
Application Information

- Generate Ideas
- Intellectual Property
- Life Sciences
- Materials
- Tech Scout
- Unparalleled Data Quality
- Higher Quality Content
- 60% Fewer Hallucinations
Browse by: Latest US Patents, China's latest patents, Technical Efficacy Thesaurus, Application Domain, Technology Topic, Popular Technical Reports.
© 2025 PatSnap. All rights reserved.Legal|Privacy policy|Modern Slavery Act Transparency Statement|Sitemap|About US| Contact US: help@patsnap.com