Steel-fiberglass composite smoke discharging facility
A technology of smoke exhaust facilities and glass fiber reinforced plastics, which is applied in the direction of building types, buildings, towers, etc., can solve problems such as chimney damage, and achieve the effects of reducing project cost, significant economic benefits, and easy processing
- Summary
- Abstract
- Description
- Claims
- Application Information
AI Technical Summary
Problems solved by technology
Method used
Image
Examples
Embodiment 1
[0032] The present invention relates to a steel-glass reinforced plastic composite smoke exhaust facility. The smoke exhaust facility is a chimney, which is composed of an inner cylinder and an outer cylinder. cylinder, that is, the glass fiber reinforced plastic inner cylinder 2). Such as figure 1 , image 3 As shown, it includes a steel outer cylinder 1 and a fiberglass (FRP) inner cylinder 2, and the diameters of the two cylinders are different; the FRP inner cylinder 2 is arranged in the matching steel outer cylinder 1; the bottom of the FRP inner cylinder 2 is placed on the steel outer cylinder. On the support ring of the cylinder 1; the glass fiber reinforced plastic inner cylinder 2 and the steel outer cylinder 1 pass the polymer foam material 3 to connect the two as image 3 The shown are organically compounded together to form a complex to achieve common force, thereby effectively saving the amount of materials used in the inner and outer cylinders, and realizing th...
Embodiment 2
[0039] The composite smoke exhaust facility of the present invention can also adopt the steel tower type, and its plan view is as follows: figure 2 As shown, the outer side of the steel outer cylinder 1 is provided with a steel tower 7. In the case of a tower-type steel chimney, the composite chimney mainly bears the vertical load, and the steel tower 7 mainly bears the horizontal load.
[0040] Others are the same as in Example 1.
Embodiment 3
[0042] In this embodiment, the composite smoke exhaust facility of the present invention can adopt the reinforced concrete sleeve type, and the outer side of the steel outer cylinder 1 is provided with a reinforced concrete outer cylinder 6, and its plan view is as follows Figure 4 , Figure 5 As shown, that is, the composite chimney mainly bears the vertical load, and the horizontal load is mainly borne by the reinforced concrete outer cylinder 6 . The steel outer cylinder 1 is a welded steel cylinder as a whole; the bottom of the glass fiber reinforced plastic inner cylinder 2 is supported by a steel support ring 5 welded on the inner wall of the steel outer cylinder 1, and the glass fiber reinforced plastic inner cylinder 2 is divided into sections by means of sockets. The inner cylinder is connected together; while the glass fiber reinforced plastic 2 and the steel outer cylinder 1 are connected by polymer foam material 3 as Figure 5 The shown are organically combined t...
PUM
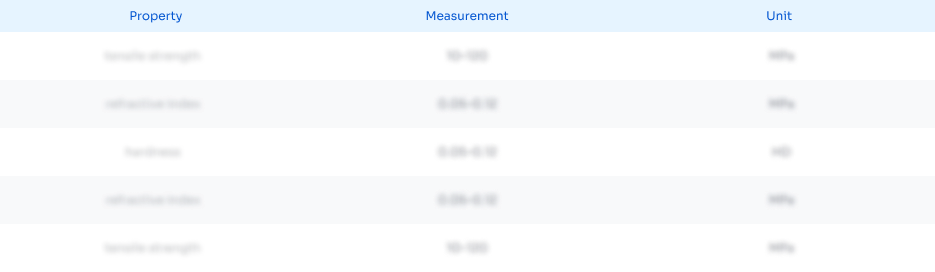
Abstract
Description
Claims
Application Information

- Generate Ideas
- Intellectual Property
- Life Sciences
- Materials
- Tech Scout
- Unparalleled Data Quality
- Higher Quality Content
- 60% Fewer Hallucinations
Browse by: Latest US Patents, China's latest patents, Technical Efficacy Thesaurus, Application Domain, Technology Topic, Popular Technical Reports.
© 2025 PatSnap. All rights reserved.Legal|Privacy policy|Modern Slavery Act Transparency Statement|Sitemap|About US| Contact US: help@patsnap.com