Charging material for blast-furnace smelting and blast-furnace smelting method
A blast furnace smelting and charge technology, applied in blast furnaces, blast furnace details, furnaces, etc., can solve the problems of lower ironmaking technical indicators, lower sinter quality, and high smelting costs, so as to improve blast furnace smelting efficiency, reduce smelting costs, and return ore low rate effect
- Summary
- Abstract
- Description
- Claims
- Application Information
AI Technical Summary
Problems solved by technology
Method used
Examples
Embodiment 1
[0040] Ordinary iron concentrates are: iron concentrates without vanadium and titanium elements
[0041] Alkaline sintered ore: in parts by weight, the alkaline sintered ore consists of 45 parts of vanadium-titanium magnetite concentrate, 8 parts of ordinary iron fine powder, 10 parts of boron-containing iron ore powder, 4 parts of SiC powder, and 8 parts of CaO. Sintered sinter raw materials. The surface of the alkaline sinter is uniformly wrapped with SiC powder whose particle size is less than 350 mesh, accounting for more than 90%. The alkalinity of the alkaline sintered ore is 2.2.5; the drum strength of the alkaline sintered ore is measured: the transfer coefficient is greater than 80%.
[0042] Acid pellets: in parts by weight, the acid pellets are composed of pellets containing 55 parts of vanadium-titanium iron concentrate, 8-10 parts of ordinary iron concentrate, 1.5 parts of magnesite, 4 parts of dolomite and 1.5 parts of bentonite Mineral raw materials are roaste...
Embodiment 2
[0046] Ordinary iron concentrates are: iron concentrates without vanadium and titanium elements
[0047] Alkaline sintered ore: in parts by weight, the alkaline sintered ore consists of 40 parts of vanadium-titanium magnetite concentrate, 5 parts of ordinary iron fine powder, 5 parts of boron-containing iron ore powder, 1 part of SiC powder, and 10 parts of CaO. Sintered raw materials are sintered. The surface of the alkaline sinter is uniformly wrapped with SiC powder whose particle size is less than 350 mesh, accounting for more than 90%. Alkalinity is: 2.3. Measuring drum strength: the conversion coefficient is greater than 80%.
[0048] Acid pellets: in parts by weight, the acid pellets are made of pellet raw materials containing 50 parts of vanadium-titanium iron concentrate, 5 parts of ordinary iron concentrate, 2 parts of magnesite, 5 parts of dolomite and 1 part of bentonite Roasted. CaO content in dolomite > 40wt%, MgO content ≥ 28wt%, SiO 2 Content <8.0wt%; Alka...
Embodiment 3
[0052] Ordinary iron concentrates are: iron concentrates without vanadium and titanium elements
[0053] Alkaline sintered ore: in parts by weight, the alkaline sintered ore consists of 50 parts of vanadium-titanium magnetite concentrate, 10 parts of ordinary iron fine powder, 15 parts of boron-containing iron ore powder, 5 parts of SiC powder, and 6 parts of CaO. Sintered sinter raw materials. The surface of the alkaline sinter is uniformly wrapped with SiC powder whose particle size is less than 350 mesh, accounting for more than 90%. Alkalinity: 2.2. Measuring drum strength: the conversion coefficient is greater than 80%.
[0054] Acid pellets: in parts by weight, the acid pellets are made of pellet raw materials containing 60 parts of vanadium-titanium iron concentrate, 10 parts of ordinary iron concentrate, 1 part of magnesite, 3 parts of dolomite and 2 parts of bentonite Roasted. CaO content in dolomite > 40wt%, MgO content ≥ 28wt%, SiO 2 Content <8.0wt%; Alkalinity...
PUM
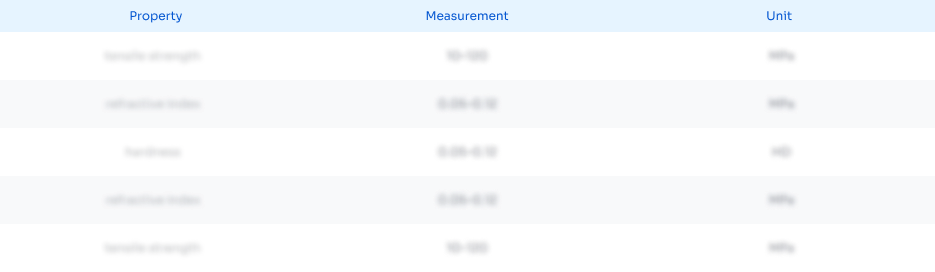
Abstract
Description
Claims
Application Information

- R&D
- Intellectual Property
- Life Sciences
- Materials
- Tech Scout
- Unparalleled Data Quality
- Higher Quality Content
- 60% Fewer Hallucinations
Browse by: Latest US Patents, China's latest patents, Technical Efficacy Thesaurus, Application Domain, Technology Topic, Popular Technical Reports.
© 2025 PatSnap. All rights reserved.Legal|Privacy policy|Modern Slavery Act Transparency Statement|Sitemap|About US| Contact US: help@patsnap.com