High-performance assembling type construction reinforcing steel bar sleeve grouting material and using method thereof
A technology for building steel bars and sleeve grouting, which is applied in construction, building components, building structures, etc., can solve the problems of the quality of grouting materials not up to standard and high price, and achieve the benefits of environmental protection, price reduction, and improvement of compressive strength Effect
- Summary
- Abstract
- Description
- Claims
- Application Information
AI Technical Summary
Problems solved by technology
Method used
Image
Examples
Embodiment 1
[0015] Embodiment 1: as figure 1 As shown, the mass ratio components of the high-performance prefabricated building steel sleeve grouting material of the present invention are: 80 parts of cement, 80 parts of quartz sand, 10 parts of mountain sand or river sand, 10 parts of expansion agent, 1 part of retarder, 0.5 part of water reducer, 1 part of defoamer, 15 parts of steel slag. The particle size of quartz sand, mountain sand or river sand, and steel slag powder is 400 mesh. Calcium sulfoaluminate is used as expansion agent, sodium gluconate is used as retarder, polycarboxylate water reducer is used as water reducer, and rosin thermal polymer is used as defoamer.
[0016] The method of using the high-performance prefabricated building reinforcement sleeve grouting material of the present invention is: under normal temperature and normal pressure, first take cement, quartz sand, mountain sand or river sand, and steel slag in proportion, and mix them evenly; then press the wei...
Embodiment 2
[0017] Embodiment 2: as figure 1 As shown, the mass ratio components of the high-performance prefabricated building steel sleeve grouting material of the present invention are: 90 parts of cement, 40 parts of quartz sand, 40 parts of mountain sand, 5 parts of expansion agent, 0.5 part of retarder, and water reducer 3 parts, 20 parts of steel slag. The particle size of quartz sand, mountain sand or river sand, and steel slag powder is 700 mesh. The expansion agent is MgO, the retarder is calcium lignosulfonate, the water reducer is phosphate, and the defoamer is petroleum sulfonate.
[0018] The method of using the high-performance prefabricated building steel sleeve grouting material of the present invention is: under normal temperature and normal pressure, first take cement, quartz sand, mountain sand, and steel slag in proportion, and mix them evenly; then press 13% of the mixture weight, Slowly add water and stir. During the stirring process, slowly add expansion agent, r...
Embodiment 3
[0019] Embodiment 3: as figure 1 As shown, the mass ratio components of the high-performance prefabricated building steel sleeve grouting material of the present invention are: 100 parts of cement, 100 parts of river sand, 15 parts of expansion agent, 2 parts of water reducing agent, 0.5 part of defoamer, and 80 parts of steel slag share. The particle size of quartz sand, mountain sand or river sand, and steel slag powder is 1000 mesh. The expansion agent is gypsum, the retarder is sodium gluconate, the water reducing agent is zinc salt, and the defoamer is hydroxyethyl methyl cellulose ether.
[0020] The method of using the high-performance prefabricated building reinforcement sleeve grouting material of the present invention is: under normal temperature and normal pressure, first take cement, quartz sand, mountain sand or river sand, and steel slag in proportion, and mix them evenly; then press the weight of the mixture 14%, slowly add water and stir, and slowly add expan...
PUM
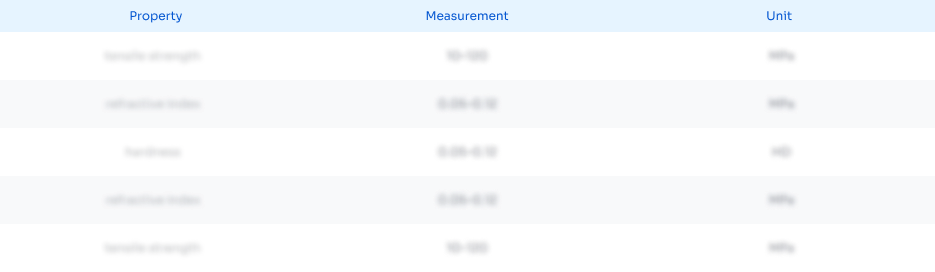
Abstract
Description
Claims
Application Information

- R&D Engineer
- R&D Manager
- IP Professional
- Industry Leading Data Capabilities
- Powerful AI technology
- Patent DNA Extraction
Browse by: Latest US Patents, China's latest patents, Technical Efficacy Thesaurus, Application Domain, Technology Topic, Popular Technical Reports.
© 2024 PatSnap. All rights reserved.Legal|Privacy policy|Modern Slavery Act Transparency Statement|Sitemap|About US| Contact US: help@patsnap.com