Method for producing graphene in green and large-scale manner
A graphene and green technology, applied in the field of green large-scale production of graphene, can solve the problems of inability to produce high-quality graphene in a green scale, limit the industrial application process of graphene, destroy the complete structure of graphene, etc., and achieve the separation method Simple and easy, fast stripping efficiency, and the effect of preserving integrity
- Summary
- Abstract
- Description
- Claims
- Application Information
AI Technical Summary
Problems solved by technology
Method used
Image
Examples
Embodiment 1
[0046] Example 1 A method for green-scale production of graphene includes the following steps:
[0047] ⑴ Prepare 300ml, 1M ammonium sulfate solution as electrolyte.
[0048] ⑵Put the anode material into the electrolytic cell filled with electrolyte and fix it with foam paper, and fix the cathode material in the foam paper.
[0049] (3) Insert the thin tube connected with the inert gas into the electrolyte and fix it on the foam paper.
[0050] ⑷Add a cooling device around the electrolyte to keep the temperature of the electrolyte at 5°C.
[0051] (5) Connect the anode and cathode of the DC power supply to the anode material and cathode material in the electrolytic cell, and the distance between the two electrodes is 1cm.
[0052] ⑹ Continuously pass inert gas protection at the anode material, turn on the power supply, and adjust the power supply voltage to 8V at the same time, start electrochemical intercalation and stripping.
[0053] ⑺ The electrochemically intercalated, peeled, and de...
Embodiment 2
[0056] Example 2 A method for green scale production of graphene, including the following steps:
[0057] ⑴ Prepare 300ml, 1M ammonium sulfate solution as electrolyte.
[0058] ⑵Put the anode material into the electrolytic cell filled with electrolyte and fix it with foam paper, and fix the cathode material in the foam paper.
[0059] (3) Insert the thin tube connected with the inert gas into the electrolyte and fix it on the foam paper.
[0060] ⑷Add a cooling device outside the electrolyte to keep the temperature of the electrolyte at 10°C.
[0061] (5) Connect the positive and negative electrodes of the DC power supply to the anode material and cathode material in the electrolytic cell, and the distance between the two electrodes is 5 cm.
[0062] ⑹ Continuously pass inert gas protection at the anode material, turn on the power supply, and adjust the power supply voltage to 20V at the same time, start electrochemical intercalation and stripping.
[0063] ⑺ The electrochemically interca...
Embodiment 3
[0066] Example 3 A method for green scale production of graphene, including the following steps:
[0067] ⑴ Prepare 300ml, 1M sodium hydroxide solution as electrolyte.
[0068] ⑵Put the anode material into the electrolytic cell filled with electrolyte and fix it with foam paper, and fix the cathode material in the foam paper.
[0069] (3) Insert the thin tube connected with the inert gas into the electrolyte and fix it on the foam paper.
[0070] ⑷Add a cooling device outside the electrolyte to keep the temperature of the electrolyte at 15°C.
[0071] (5) Connect the positive and negative electrodes of the DC power supply to the anode material and cathode material in the electrolytic cell, and the distance between the two electrodes is 2 cm.
[0072] ⑹ Pass inert gas protection at the anode material, turn on the power supply, and adjust the power supply voltage to 10V at the same time, start electrochemical intercalation and stripping.
[0073] ⑺ The electrochemically intercalated, peeled...
PUM
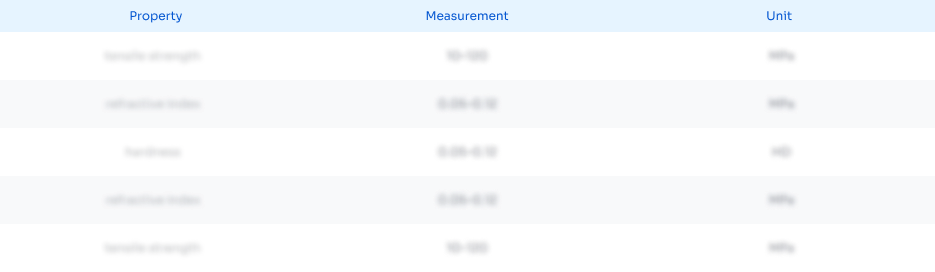
Abstract
Description
Claims
Application Information

- Generate Ideas
- Intellectual Property
- Life Sciences
- Materials
- Tech Scout
- Unparalleled Data Quality
- Higher Quality Content
- 60% Fewer Hallucinations
Browse by: Latest US Patents, China's latest patents, Technical Efficacy Thesaurus, Application Domain, Technology Topic, Popular Technical Reports.
© 2025 PatSnap. All rights reserved.Legal|Privacy policy|Modern Slavery Act Transparency Statement|Sitemap|About US| Contact US: help@patsnap.com