Method for evaluating propriety of molding sheared edge
An evaluation method and edge technology, which is applied in the direction of testing the ductility of materials, etc., can solve the problems of unclear molding, material edge application without any consideration, etc., and achieve the effect of preventing adverse effects
- Summary
- Abstract
- Description
- Claims
- Application Information
AI Technical Summary
Problems solved by technology
Method used
Image
Examples
no. 1 Embodiment approach
[0076] Next, the method of evaluating whether the cut edge can be shaped according to this embodiment will be described with reference to the drawings.
[0077] The method for evaluating whether or not the cut edge can be shaped according to the present embodiment is a technique for evaluating whether or not the cut edge can be shaped with respect to a metal plate after one-time molding (pre-forming).
[0078]
[0079] Such as Figure 13 As shown, the moldability evaluation method of the present embodiment includes an experimental data acquisition step 1, a pre-deformation and other effect variable setting step 2, a moldable area determination step 3, a molding specification data acquisition step 4, and a moldability determination step 5.
[0080] In the experimental data acquisition step 1, a hole expansion test is performed on the metal plate that has been subjected to a preset preform. In the hole expansion test, two or more kinds of hole expansion tests with different radial stra...
no. 2 Embodiment approach
[0129] Next, the second embodiment will be described with reference to the drawings. The same components as those of the first embodiment will be described with the same reference numerals.
[0130] Such as Figure 16 As shown, the moldability evaluation method of this embodiment includes: experimental data acquisition process without pre-forming conditions 7, process of determining moldable areas without pre-forming conditions 8, conversion process to post-preforming conversion process 9, molding The specification data acquisition step 4 and the determination step 5 are possible.
[0131] In step 7 of obtaining experimental data without preforming, a hole reaming test is performed on the metal plate without preforming (the metal plate before preforming) to obtain the radial strain gradient at the shear edge and the Multiple data with different strain gradients with effect variables such as the deformation limit of the metal plate as parameters.
[0132] In step 8 of determining th...
PUM
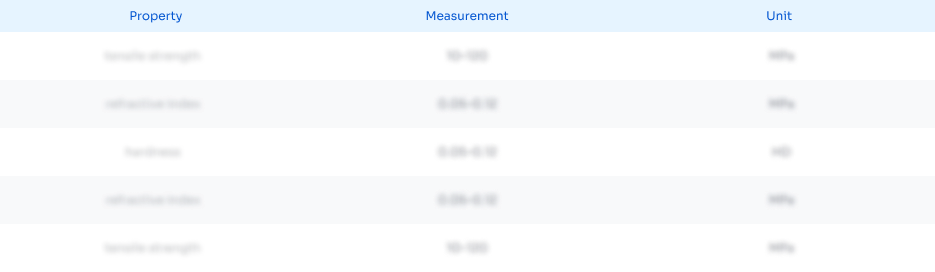
Abstract
Description
Claims
Application Information

- R&D
- Intellectual Property
- Life Sciences
- Materials
- Tech Scout
- Unparalleled Data Quality
- Higher Quality Content
- 60% Fewer Hallucinations
Browse by: Latest US Patents, China's latest patents, Technical Efficacy Thesaurus, Application Domain, Technology Topic, Popular Technical Reports.
© 2025 PatSnap. All rights reserved.Legal|Privacy policy|Modern Slavery Act Transparency Statement|Sitemap|About US| Contact US: help@patsnap.com