Crankshaft connecting rod cap assembly of cold header and mounting method thereof
A technology of crankshaft connecting rod and installation method, applied in the directions of engine components, engine lubrication, shafts, etc., can solve the problems of affecting the operation accuracy, affecting the accuracy, and the lubricating oil being easily taken out, so as to avoid the increase of friction and improve the The effect of heat dissipation
- Summary
- Abstract
- Description
- Claims
- Application Information
AI Technical Summary
Problems solved by technology
Method used
Image
Examples
Embodiment 1
[0028] Such as figure 1 As shown, the crankshaft connecting rod cover assembly of a cold heading machine provided by this embodiment includes a body 1, and the connecting rod installation through hole 6 is arranged in the body 1, and the two axial ends of the connecting rod installation through hole 6 are More than two copper sleeves 7 are distributed at intervals, and an oil groove 8 is arranged on the inner wall of each copper sleeve 7 . In this embodiment, two copper sleeves 7 are distributed at the two axial ends of the connecting rod installation through hole 6 at intervals, and there is a distance of a certain length between the two copper sleeves 7. The number of copper sleeves 7 here is not correct for this embodiment The limitation of the invention is only considered as a preferred solution, and 3, 5 or more can be set in a specific embodiment.
[0029] This embodiment also discloses a method for installing a crankshaft connecting rod cover assembly of a cold heading...
Embodiment 2
[0032] Such as Figure 2 to Figure 5 As shown, this embodiment provides a crankshaft connecting rod cover assembly for a cold heading machine, the body 1 includes a detachably connected connecting rod left cover 2 and a connecting rod right cover 3, and a connecting rod left cover 2 is provided. There is a semi-cylindrical first semi-cylindrical groove 4 and the first ear side 12 positioned at the top and bottom of the connecting rod left cover 2, and a semi-cylindrical second semi-cylindrical groove 5 and a semi-cylindrical second semi-cylindrical groove 5 positioned at the right side of the connecting rod are arranged on the connecting rod right cover 3. The second ear side 13 on the top and bottom of the cover 3, the first ear side 12 and the second ear side 13 are matched by fasteners, and the connecting rod installation through hole 6 is formed by the first semi-cylindrical groove 4 and the second semi-cylindrical groove 4. The structure formed after the groove 5 is synth...
Embodiment 3
[0036] Such as Figure 6As shown, the general structure of the crankshaft connecting rod cover assembly of a cold heading machine provided by this embodiment is the same as that of Embodiment 2, the difference is that, in order to facilitate processing, the oil groove 8 is formed by a longitudinal groove 14 and a longitudinal groove 14, more than one horizontal groove 15 is distributed at intervals for cross distribution, and the intersections of the vertical groove 14 and the horizontal groove 15 are connected to each other. Through such an oil groove, the distribution of the oil groove 8 is more uniform than that of a fishnet, and the heat dissipation effect is improved.
PUM
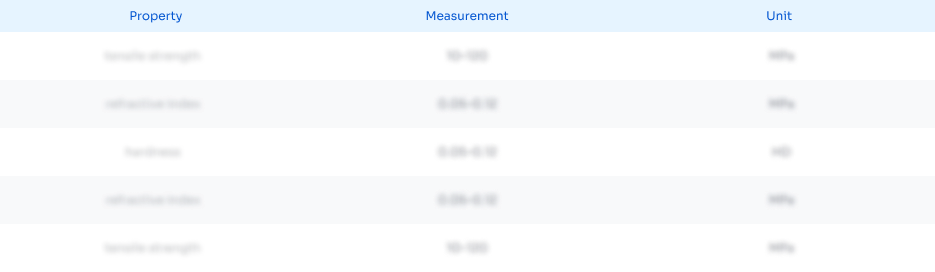
Abstract
Description
Claims
Application Information

- R&D Engineer
- R&D Manager
- IP Professional
- Industry Leading Data Capabilities
- Powerful AI technology
- Patent DNA Extraction
Browse by: Latest US Patents, China's latest patents, Technical Efficacy Thesaurus, Application Domain, Technology Topic, Popular Technical Reports.
© 2024 PatSnap. All rights reserved.Legal|Privacy policy|Modern Slavery Act Transparency Statement|Sitemap|About US| Contact US: help@patsnap.com