Method and system for preparing lime from waste artificial engineered stones
A technology of artificial granite and lime, which is applied in the field of making lime from waste artificial granite, can solve the problems of artificial granite being difficult to reuse, occupying land area, and low lime purity, so as to achieve good lime quality, resource saving and high purity. Effect
- Summary
- Abstract
- Description
- Claims
- Application Information
AI Technical Summary
Problems solved by technology
Method used
Image
Examples
Embodiment 1
[0046] The waste artificial granite is sent to the pulverizer 120 to be pulverized into artificial granite powder, and the powder is sent to the pre-burning furnace 110 and burned for 2 hours under the environment of 300°C to remove the organic resin. The generated gas passes into the waste gas absorbing device 111, and the waste gas absorbing device 111 contains lye to remove the tail gas. After burning, it is transported to the first mixed reaction tank 140 to react with the nitric acid solution with a mass concentration of 25%. The mass ratio of the waste artificial granite powder after burning to the nitric acid solution is 1:47.5, and the reaction time is 40min. The solid-liquid mixture is passed through the first filter 150 for filtration to obtain the first filter residue and the first solution. The first filter residue is burned in the third calcination furnace 130 at 150° C. to obtain silica, and the two Silica recovery. Pass the first solution into the second mixing...
Embodiment 2
[0048] The waste artificial granite is sent to the pulverizer 120 to be crushed into artificial granite powder, and the powder is sent to the pre-burning furnace 110 and burned for 1 hour at 700°C to remove the organic resin. The generated gas passes into the waste gas absorbing device 111, and the waste gas absorbing device 111 contains lye to remove the tail gas. After burning, it is transported to the first mixed reaction tank 140 to react with nitric acid solution with a mass concentration of 32%. The mass ratio of the waste artificial granite powder after burning to the nitric acid solution is 1:37, and the reaction time is 200min. The solid-liquid mixture is passed through the first filter 150 for filtration to obtain the first filter residue and the first solution, and the first filter residue is burned in the third calcination furnace 130 at 200°C to obtain silica, and the two Silica recovery. Pass the first solution into the second mixing reaction tank 160, add sodiu...
Embodiment 3
[0050] The waste artificial granite is sent to the pulverizer 120 to be crushed into artificial granite powder, and the powder is sent to the pre-burning furnace 110 and burned for 1.5 hours at 500°C to remove the organic resin. The generated gas passes into the waste gas absorbing device 111, and the waste gas absorbing device 111 contains lye to remove the tail gas. After burning, it is transported to the first mixed reaction tank 140 to react with the nitric acid solution with a mass concentration of 28%. The mass ratio of the waste artificial granite powder after burning to the nitric acid solution is 1:40, and the reaction time is 60min. The solid-liquid mixture is passed through the first filter 150 for filtration to obtain the first filter residue and the first solution. The first filter residue is burned in the third calcination furnace 130 at 170° C. to obtain silica, and the two Silica recovery. Pass the first solution into the second mixing reaction tank 160, add s...
PUM
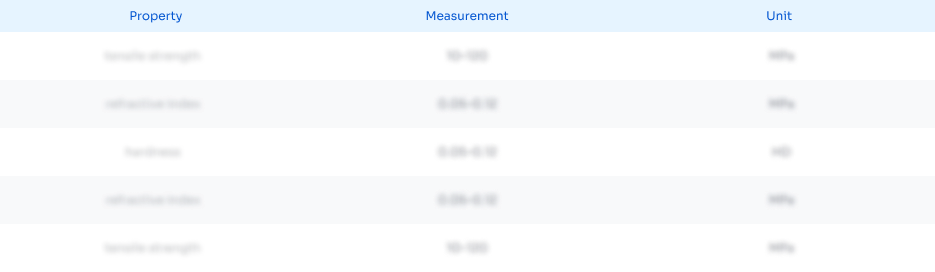
Abstract
Description
Claims
Application Information

- R&D Engineer
- R&D Manager
- IP Professional
- Industry Leading Data Capabilities
- Powerful AI technology
- Patent DNA Extraction
Browse by: Latest US Patents, China's latest patents, Technical Efficacy Thesaurus, Application Domain, Technology Topic, Popular Technical Reports.
© 2024 PatSnap. All rights reserved.Legal|Privacy policy|Modern Slavery Act Transparency Statement|Sitemap|About US| Contact US: help@patsnap.com