Laser molding method of extra/ultra high-voltage circuit tool
An ultra-high voltage and laser forming technology, applied in the field of parts manufacturing, can solve problems such as spheroidization, cracks, delamination, etc., achieve excellent wear resistance and corrosion resistance, simple process, and reduce production costs.
- Summary
- Abstract
- Description
- Claims
- Application Information
AI Technical Summary
Problems solved by technology
Method used
Image
Examples
Embodiment approach
[0039] As a preferred embodiment of the present invention, the cooling of the test piece is carried out in stages: in the first stage, after the test piece is formed, it is cooled at 100-120°C per hour until it is cooled to about 800°C and kept at 30-50°C. Minutes; in the second stage, cool down at 120-160°C per hour until it cools to about 500°C, and keep for 50-70 minutes; in the third stage, cool down at 140-180°C per hour until it cools to room temperature.
[0040] As a preferred embodiment of the present invention, when the laser is irradiated, the laser beam is irradiated on the titanium alloy material in a horizontal stripe shape, a vertical stripe shape or a checkerboard shape.
[0041] As a preferred embodiment of the present invention, the surface of the cleaning material is ultrasonically cleaned by placing the titanium alloy in absolute ethanol.
PUM
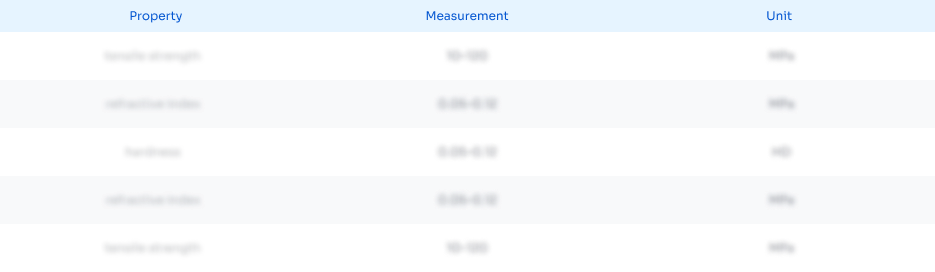
Abstract
Description
Claims
Application Information

- R&D Engineer
- R&D Manager
- IP Professional
- Industry Leading Data Capabilities
- Powerful AI technology
- Patent DNA Extraction
Browse by: Latest US Patents, China's latest patents, Technical Efficacy Thesaurus, Application Domain, Technology Topic, Popular Technical Reports.
© 2024 PatSnap. All rights reserved.Legal|Privacy policy|Modern Slavery Act Transparency Statement|Sitemap|About US| Contact US: help@patsnap.com