Multi-station injection moulding machine
An injection molding machine and multi-station technology, which is applied in the field of multi-station injection molding machines, can solve the problems of inability to carry out injection molding work, limited number of settings, and inability to set up in batches, so as to reduce production costs and labor costs, and reduce occupied space , The effect of improving injection molding efficiency
- Summary
- Abstract
- Description
- Claims
- Application Information
AI Technical Summary
Problems solved by technology
Method used
Image
Examples
Embodiment Construction
[0026] The present invention will be further described below with specific embodiment, see figure 1 -6:
[0027] A multi-station injection molding machine, comprising an extruder 1, the discharge port of the extruder 1 is connected to the material storage cylinder 3 through a feeding main pipe 2, and several discharge ports 4 are arranged on the feeding main pipe 2, each The outlets 4 are all connected with clamping frames 5 , and several clamping frames 5 are arranged along at least one side of the extruder 1 . The arrangement of the clamping frame 5 is designed according to specific conditions, and can be arranged on one side of the extruder 1, or can be arranged around the extruder 1. The melt raw material extruded by the extruder 1 enters the feeding main pipe 2 and the storage cylinder 3 , and is pressurized by the storage cylinder 3 so that the melt raw material is sent from the discharge port 4 into the clamping frame 5 .
[0028] Specifically, the feeding main pipe 2...
PUM
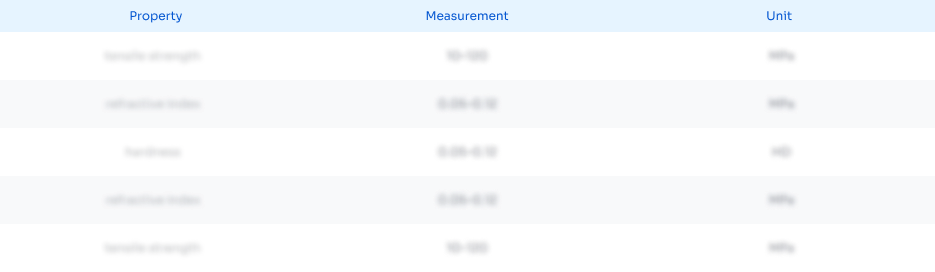
Abstract
Description
Claims
Application Information

- R&D Engineer
- R&D Manager
- IP Professional
- Industry Leading Data Capabilities
- Powerful AI technology
- Patent DNA Extraction
Browse by: Latest US Patents, China's latest patents, Technical Efficacy Thesaurus, Application Domain, Technology Topic, Popular Technical Reports.
© 2024 PatSnap. All rights reserved.Legal|Privacy policy|Modern Slavery Act Transparency Statement|Sitemap|About US| Contact US: help@patsnap.com