Finish coat material and preparation method thereof
A technology of facing layer and hot-melt resin, which is applied in coatings, fireproof coatings, antifouling/underwater coatings, etc., can solve the problems of complex preparation process, easy cracking, high temperature resistance, and poor aging resistance. Achieve the effect of simple preparation method, good temperature resistance and good weather resistance
- Summary
- Abstract
- Description
- Claims
- Application Information
AI Technical Summary
Problems solved by technology
Method used
Examples
Embodiment 1
[0021] The material components of the facing layer include 20 parts by weight of hot-melt resin, 10 parts of silicone acrylic emulsion, 5 parts of inorganic thickener, 5 parts of anti-crack fiber, 2 parts of foaming agent, polycarboxylic acid high-performance water-reducing 3 parts of agent, 5 parts of silica powder, 2 parts of ultraviolet absorber, 2 parts of flame retardant, 1 part of defoamer, 3 parts of hydroxypropyl methylcellulose, 2 parts of lignocellulose, and 5 parts of kaolin.
[0022] The preparation method of the present embodiment comprises the following steps:
[0023] A. Mix the hot-melt resin, silicon-acrylic emulsion, inorganic thickener, and anti-cracking fiber and then add it to the mixer for mixing. The mixing temperature is 50°C and the mixing time is 30 minutes to obtain the mixture A;
[0024] B. Mix the foaming agent, polycarboxylate high-performance water reducer, silicon micropowder, ultraviolet absorber, flame retardant, defoamer, hydroxypropyl methy...
Embodiment 2
[0028] The material components of the facing layer include 40 parts by weight of hot-melt resin, 30 parts of silicone acrylic emulsion, 10 parts of inorganic thickener, 15 parts of anti-crack fiber, 8 parts of foaming agent, polycarboxylic acid high-performance water-reducing 10 parts of agent, 15 parts of silica powder, 8 parts of ultraviolet absorber, 10 parts of flame retardant, 4 parts of defoamer, 12 parts of hydroxypropyl methylcellulose, 8 parts of lignocellulose, and 15 parts of kaolin.
[0029] The preparation method of the present embodiment comprises the following steps:
[0030] A. Mix the hot-melt resin, silicone acrylic emulsion, inorganic thickener, and anti-cracking fiber and then add it to the mixer for mixing. The mixing temperature is 80°C and the mixing time is 50 minutes to obtain the mixture A;
[0031] B. Mix the foaming agent, polycarboxylate high-performance water reducer, silicon micropowder, ultraviolet absorber, flame retardant, defoamer, hydroxypro...
Embodiment 3
[0035] The material components of the facing layer include 22 parts by weight of hot-melt resin, 12 parts of silicone acrylic emulsion, 6 parts of inorganic thickener, 6 parts of anti-crack fiber, 3 parts of foaming agent, polycarboxylic acid high-performance water-reducing 4 parts of agent, 6 parts of silica powder, 3 parts of ultraviolet absorber, 3 parts of flame retardant, 2 parts of defoamer, 4 parts of hydroxypropyl methylcellulose, 3 parts of lignocellulose, and 6 parts of kaolin.
[0036] The preparation method of the present embodiment comprises the following steps:
[0037] A. Mix the hot-melt resin, silicon-acrylic emulsion, inorganic thickener, and anti-cracking fiber and then add it to the mixer for mixing. The mixing temperature is 55°C and the mixing time is 32 minutes to obtain the mixture A;
[0038] B. Mix the foaming agent, polycarboxylate high-performance water reducer, silicon micropowder, ultraviolet absorber, flame retardant, defoamer, hydroxypropyl meth...
PUM
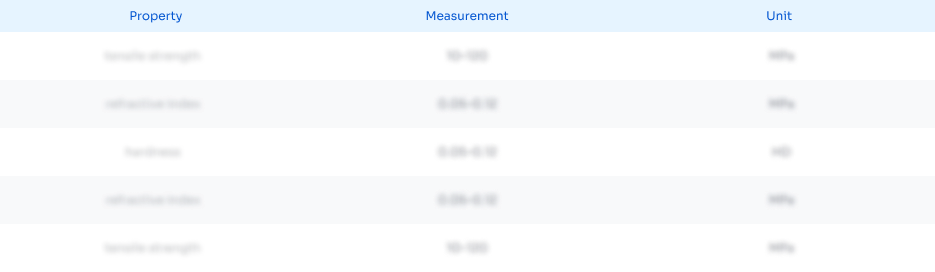
Abstract
Description
Claims
Application Information

- R&D Engineer
- R&D Manager
- IP Professional
- Industry Leading Data Capabilities
- Powerful AI technology
- Patent DNA Extraction
Browse by: Latest US Patents, China's latest patents, Technical Efficacy Thesaurus, Application Domain, Technology Topic, Popular Technical Reports.
© 2024 PatSnap. All rights reserved.Legal|Privacy policy|Modern Slavery Act Transparency Statement|Sitemap|About US| Contact US: help@patsnap.com