Converter baking method performed after 120t converter replaces furnace lining refractory material
A furnace lining refractory material and furnace method technology, which is applied in the direction of manufacturing converters, etc., can solve the problems of furnace body bursting, poor furnace effect, shortened furnace lining life, etc. Life extension effect
- Summary
- Abstract
- Description
- Claims
- Application Information
AI Technical Summary
Problems solved by technology
Method used
Image
Examples
Embodiment Construction
[0025] A method for drying a 120t converter after replacing the refractory lining of the furnace, the method comprises the following operation steps:
[0026] (1) Add 8 tons of large coke and 1 ton of waste wood into the furnace before the oven, and use cotton yarn soaked in diesel oil to ignite and put in from the furnace mouth to ignite the wood.
[0027] (2) After blowing oxygen through the gun and waiting for the wood to catch fire, add coke to the furnace in batches from the silo on the top of the furnace. The first batch of coke is divided into 3 times within the first 120 minutes, adding 1 ton each time, and the interval is 40 minutes, a total of 3 tons of coke was added, and then 0.5t of coke was added every 20 minutes, and the oven time was about 3 hours.
[0028] (3) Control of oxygen flow, set the flow at 5000m3 / h before the gun is fired, and adjust the flow to 8000m3 / h according to the baking time, gun position and coke combustion conditions, and the flow remains b...
PUM
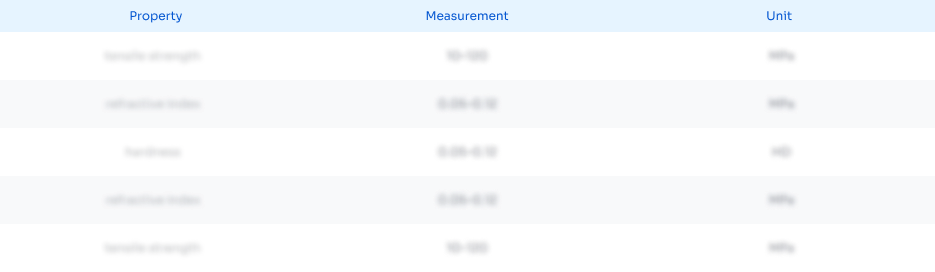
Abstract
Description
Claims
Application Information

- R&D
- Intellectual Property
- Life Sciences
- Materials
- Tech Scout
- Unparalleled Data Quality
- Higher Quality Content
- 60% Fewer Hallucinations
Browse by: Latest US Patents, China's latest patents, Technical Efficacy Thesaurus, Application Domain, Technology Topic, Popular Technical Reports.
© 2025 PatSnap. All rights reserved.Legal|Privacy policy|Modern Slavery Act Transparency Statement|Sitemap|About US| Contact US: help@patsnap.com