Automatic cleaning facility for rocket storage tank structure
A technology for cleaning equipment and storage tanks, which is used in the cleaning and cleaning of slender tank structures, and in the field of automated cleaning equipment, which can solve the problems of unguaranteed quality and low cleaning efficiency.
- Summary
- Abstract
- Description
- Claims
- Application Information
AI Technical Summary
Problems solved by technology
Method used
Image
Examples
Embodiment approach 1
[0042] to combine figure 1 Describe this embodiment, an automatic cleaning device with a storage tank structure in this embodiment, the automatic cleaning device includes a cleaning head 1, an autorotation mechanism 2, a feeding mechanism 3, a horizontal telescopic mechanism 4, a rotary mechanism 5, and a vertical telescopic mechanism 6. Base frame 8; wherein: a vertical telescopic mechanism 6 is fixed above the bottom frame 8; a rotary mechanism 5 is fixed at the telescopic end of the vertical telescopic mechanism 6; a horizontal telescopic mechanism 4 is fixed on the top of the rotary mechanism 5 for driving horizontal telescopic The mechanism 4 rotates 360° in the horizontal plane; the telescopic end of the horizontal telescopic mechanism 4 is connected to the feed mechanism 3; the telescopic end of the feed mechanism 3 is connected to the rotation mechanism 2 for driving the rotation mechanism 2 to reciprocate in the vertical direction ; The bottom end of the rotation mech...
Embodiment approach 2
[0055] In this embodiment, on the basis of Embodiment 1, the structure of the feed mechanism 3 is further limited. In this embodiment, the feed mechanism 3 includes a winch 31, a wire rope 32, a pulley 33 and a feed telescopic arm device 34; wherein: The telescopic arm device 34 is a telescopic sleeve structure composed of n sections of feed arms, wherein: n≥2, the feed arm positioned at the outermost layer is the basic feed arm 341, and the feed arm positioned at the innermost layer is the feed arm 341. n section arm; winch 31 is fixed on the side wall of feeding basic arm 341; Pulley 33 is fixed on the top of feeding basic arm 341; The feeding n-section arm is connected; the hoist 31 pulls the wire rope 32 to drive the feeding n-section arm to reciprocate in the vertical direction.
[0056] The feeding mechanism 3 in this embodiment realizes the feeding in the height direction of the cleaning head 1, and the structure of the feeding mechanism 3 is as follows: Figure 4-6 s...
Embodiment approach 3
[0061] On the basis of the second embodiment, this embodiment adds the technical feature "in the n-section feed arm, a guide wheel is arranged between two adjacent feed arms", such as Figure 4-6 As shown, among the n-section feed arms added in this embodiment, a guide wheel is arranged between two adjacent feed arms, which is to change the sliding friction slider of the traditional telescopic arm into a rolling friction guide wheel, and obtain In order to reduce the resistance of the falling of each section of the arm, reduce friction, save energy, and can also achieve the effect of prolonging the service life and reducing costs, and can also overcome the sliding friction of the traditional telescopic arm. In order to solve the problem of poor stability of the telescopic arm caused by damage, this embodiment adopts a rolling friction guide wheel to make the telescopic arm have better stability.
PUM
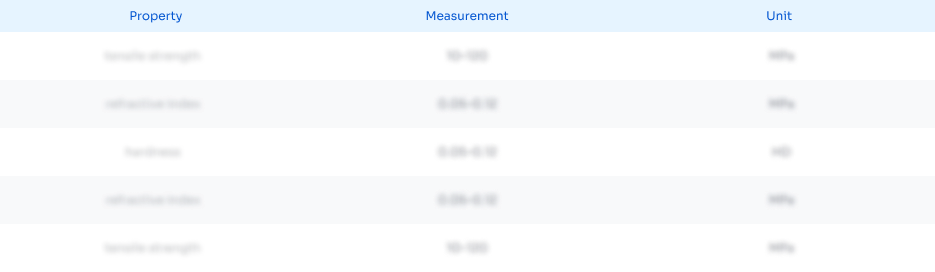
Abstract
Description
Claims
Application Information

- Generate Ideas
- Intellectual Property
- Life Sciences
- Materials
- Tech Scout
- Unparalleled Data Quality
- Higher Quality Content
- 60% Fewer Hallucinations
Browse by: Latest US Patents, China's latest patents, Technical Efficacy Thesaurus, Application Domain, Technology Topic, Popular Technical Reports.
© 2025 PatSnap. All rights reserved.Legal|Privacy policy|Modern Slavery Act Transparency Statement|Sitemap|About US| Contact US: help@patsnap.com