Zirconium silicate-mullite composite wear-resisting castable and preparation method thereof
A technology of mullite and zirconium silicate, which is applied in the field of refractory materials, can solve problems such as insufficient vibrator vibration, structural damage, and shortened service life of coal injection pipes, achieve good high temperature volume stability, increase load softening temperature, and compensate for tissue Effects of Structural Defects
- Summary
- Abstract
- Description
- Claims
- Application Information
AI Technical Summary
Problems solved by technology
Method used
Image
Examples
Embodiment 1
[0021] A zirconium silicate-mullite composite wear-resistant castable, including the following components and parts by weight: 10 parts of 5-8mm mullite, 5 parts of 3-5mm mullite, and 5 parts of 1-3mm mullite , 6 parts of 3-5mm andalusite particles, 5.1 parts of andalusite-sillimanite composite mineral powder with a particle size of less than 0.075mm, and ZrO with a particle size of less than 1μm 2 5 parts, silicon micropowder with particle size less than 1 μm 3 parts, Al with particle size less than 1.2 μm 2 o 3 3 parts of micro powder, 3 parts of calcium aluminate cement, 0.15 parts of sodium hexametaphosphate, 0.08 parts of leveling agent, 0.5 parts of heat-resistant steel fiber, and 0.2 part of explosion-proof fiber.
[0022] Prepare the castable according to the following steps: Pour the raw materials of the above castable into the stirring device, stir and mix at room temperature, add 4% water and stir evenly, pour into the mold, maintain for 48 hours with the mold, an...
Embodiment 2
[0024] A zirconium silicate-mullite composite wear-resistant castable, including the following components and parts by weight: 9 parts of 5-8mm mullite, 8 parts of 3-5mm mullite, 4 parts of 1-3mm mullite , 7 parts of andalusite particles of 3-5mm, 6 parts of andalusite-sillimanite composite mineral powder with a particle size of less than 0.075mm, and ZrO with a particle size of less than 1μm 2 5 parts, silicon powder with particle size less than 1 μm 4 parts, Al with particle size less than 1.2 μm 2 o 3 4 parts of micro powder, 4 parts of calcium aluminate cement, 0.16 parts of sodium hexametaphosphate, 0.09 parts of leveling agent, 0.7 parts of heat-resistant steel fiber, and 0.2 part of explosion-proof fiber.
[0025] Prepare the castable according to the following steps: Pour the raw materials of the above castable into the stirring device, stir and mix at room temperature, add 4% water and stir evenly, pour into the mold, cure with the mold for 48 hours, and dry after d...
Embodiment 3
[0027] A zirconium silicate-mullite composite wear-resistant castable, comprising the following components and parts by weight: 8 parts of 5-8mm mullite, 8 parts of 3-5mm mullite, 6 parts of 1-3mm mullite , 8 parts of 3-5mm andalusite particles, 7.2 parts of andalusite-sillimanite composite mineral powder with a particle size of less than 0.075mm, and ZrO with a particle size of less than 1μm 2 6 parts, microsilica powder with particle size less than 1 μm 5 parts, Al with particle size less than 1.2 μm 2 o 3 4 parts of micro powder, 5 parts of calcium aluminate cement, 0.17 parts of sodium hexametaphosphate, 0.10 parts of leveling agent, 1.0 parts of heat-resistant steel fiber, and 0.2 parts of explosion-proof fiber.
[0028] Prepare the castable according to the following steps: pour the raw materials of the above castable into the stirring device, stir and mix at room temperature, add 4% water and stir evenly, pour into the mold, maintain for 48 hours with the mold, and dr...
PUM
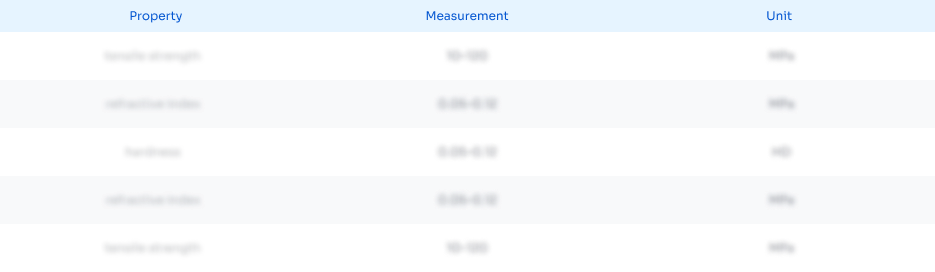
Abstract
Description
Claims
Application Information

- Generate Ideas
- Intellectual Property
- Life Sciences
- Materials
- Tech Scout
- Unparalleled Data Quality
- Higher Quality Content
- 60% Fewer Hallucinations
Browse by: Latest US Patents, China's latest patents, Technical Efficacy Thesaurus, Application Domain, Technology Topic, Popular Technical Reports.
© 2025 PatSnap. All rights reserved.Legal|Privacy policy|Modern Slavery Act Transparency Statement|Sitemap|About US| Contact US: help@patsnap.com