A construction method for off-site hoisting of super-large-span tension truss
A string truss and construction method technology, applied in the processing of building materials, construction, building construction, etc., can solve the problems of structural damage of water delivery corridors, unsuitable for large-scale hoisting equipment, etc., to achieve cost-saving measures, considerable Economic and social benefits, high positioning accuracy
- Summary
- Abstract
- Description
- Claims
- Application Information
AI Technical Summary
Problems solved by technology
Method used
Examples
Embodiment 1
[0042] An off-site hoisting construction method of a super-large-span string truss comprising the following steps:
[0043] (1) Precisely blank and process the upper chord, lower chord, and web of the tension truss through the structural form-finding method, and send it to the construction site outside the construction site;
[0044] (2) According to the span of the string truss to be constructed, the truss sections are assembled in sections on the tooling tire frame in a horizontal manner, and the adjacent truss sections are assembled into a complete single truss through connecting plates and bolts; then Install sliding shoes at the bottom of the supports at both ends of each truss;
[0045] (3) According to the length and span of the string truss to be constructed, two parallel rows of concrete columns are first poured on the construction site, and the sliding beam is installed in the gap between the two concrete columns so that the sliding beam and the concrete column Equal ...
Embodiment 2
[0060] The structural plane size of the Port Channel Sediment Engineering and Transportation Industry Key Laboratory of Estuary and Coastal Deep Water Channel Test Hall is 121.6m×201.2m. m, mid-span spacing is 12m, the steel roof is composed of 18 horizontal string beam trusses and 9 longitudinal connection secondary trusses, and all trusses and roof supports are composed of steel pipe members.
[0061] The specific off-site hoisting construction method is as follows:
[0062] (1) Precisely blank and process the upper chord, lower chord, and web of the tension truss through the structural form-finding method, and send it to the construction site outside the construction site;
[0063] (2) According to the span of the string truss to be constructed, 9 truss sections are assembled on the tooling frame in a horizontal manner, and the adjacent truss sections are assembled into a complete single truss through connecting plates and bolts Truss; then install sliding shoes at the bot...
PUM
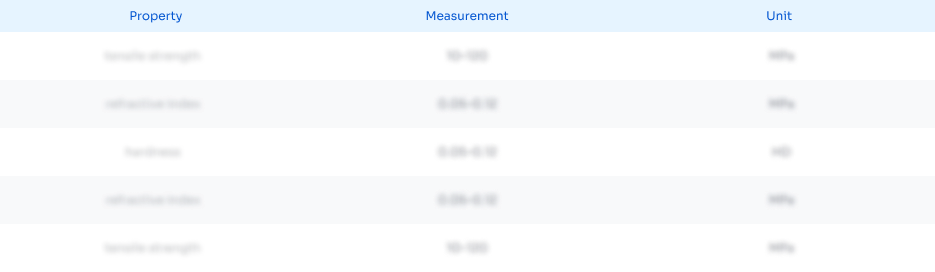
Abstract
Description
Claims
Application Information

- Generate Ideas
- Intellectual Property
- Life Sciences
- Materials
- Tech Scout
- Unparalleled Data Quality
- Higher Quality Content
- 60% Fewer Hallucinations
Browse by: Latest US Patents, China's latest patents, Technical Efficacy Thesaurus, Application Domain, Technology Topic, Popular Technical Reports.
© 2025 PatSnap. All rights reserved.Legal|Privacy policy|Modern Slavery Act Transparency Statement|Sitemap|About US| Contact US: help@patsnap.com