Novel conductive slag for casting and the preparation method thereof
A conductive slag, a new type of technology, is applied in the field of new conductive slag for electroslag and its preparation, which can solve the problems of low cost, high cost of titanium conductive slag, and difficulty in crushing, so as to avoid titanium nitride inclusions, low price, The effect of improving quality
- Summary
- Abstract
- Description
- Claims
- Application Information
AI Technical Summary
Problems solved by technology
Method used
Image
Examples
Embodiment 1
[0016] A new type of conductive slag for electroslag, which is specifically composed of graphite powder, carbon steel shavings and water glass, mixed according to weight percentage, the mixing ratio of graphite powder is 40%, and the mixing ratio of carbon steel shavings 40%, the water glass mixing ratio is 20%, and the weight percentages of the three add up to 100%. Water glass is used as a binder, and carbon steel steel chips are first crushed into powder in a steel chip crusher.
Embodiment 2
[0018] A new type of conductive slag for electroslag, which is specifically composed of graphite powder mixed with carbon steel shavings and water glass, mixed by weight percentage, the mixing ratio of graphite powder is 42%, and the mixing ratio of carbon steel shavings 43%, the water glass mixing ratio is 15%, and the weight percentage of the three is added to 100%. Water glass is used as a binder, and the carbon steel shavings are first crushed into powder in a steel shavings crusher.
Embodiment 3
[0020] A new type of conductive slag for electroslag, which is specifically composed of graphite powder, carbon steel shavings and water glass, mixed according to weight percentage, the mixing ratio of graphite powder is 36%, and the mixing ratio of carbon steel shavings is 36%. The mixing ratio of water glass is 38%, and the mixing ratio of water glass is 26%. The weight percentage of the three is added to be 100%.
[0021] Firstly, the water glass needs to be diluted with water, the ratio of water glass to water is 50%, graphite powder and carbon steel shavings are first mixed in proportion, then the diluted water glass is added and stirred evenly, and the special mold equipment is used for production.
[0022] The special mold (see the illustration for details) figure 1 ) is a wooden material, in the form of a cuboid, with a length and width of 120mm and a height of 40mm, and consists of two parts, each of which includes a mold 2 and a clamp 3, with an inner hole 1 in the m...
PUM
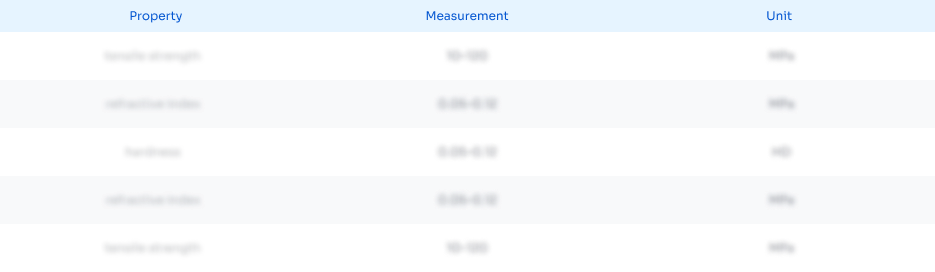
Abstract
Description
Claims
Application Information

- R&D Engineer
- R&D Manager
- IP Professional
- Industry Leading Data Capabilities
- Powerful AI technology
- Patent DNA Extraction
Browse by: Latest US Patents, China's latest patents, Technical Efficacy Thesaurus, Application Domain, Technology Topic, Popular Technical Reports.
© 2024 PatSnap. All rights reserved.Legal|Privacy policy|Modern Slavery Act Transparency Statement|Sitemap|About US| Contact US: help@patsnap.com