Coating material for improving low temperature explosion performance of PVC slush molded skin, and spraying method thereof
A coating material and skin technology, applied in coatings, polyurea/polyurethane coatings, etc., can solve problems such as unsatisfactory spraying effect, skin cracking, construction difficulties, etc., to reduce design constraints, solve chipping, spraying temperature Wide range of effects
- Summary
- Abstract
- Description
- Claims
- Application Information
AI Technical Summary
Problems solved by technology
Method used
Image
Examples
Embodiment 1
[0043] Coating material ratio: water-based polyurethane 85 wt%, color paste wt 5%, film-forming aid (dipropylene glycol methyl ether) wt4%, defoamer (water-based molecular grade defoamer) 0.2 wt%, wetting agent ( Alkyne diol ethoxylate) 0.4 wt%, thickener (water-based polyurethane thickener) 0.4 wt%, and the rest is water.
[0044] Coating preparation method:
[0045] Step 1. Add 50 grams of color paste to 850 grams of pure water-based polyurethane paint (APU-390), stir and mix well;
[0046] Step 2. Mix 40 grams of film-forming aids and 50 grams of water into the system of step 1, stir and mix well.
[0047] Step 3. Add 2 grams of defoamer to the system in step 2, stir and mix well.
[0048] Step 4. Add 4 grams of wetting agent to the system in step 3, and mix well.
[0049] Step 5. Add 4 grams of thickener to the system in step 4, stir and mix well.
[0050] Step 6. Take an appropriate amount of the compounded paint and add it to the spray gun for use.
[0051] Spraying...
Embodiment 2
[0055] Coating material ratio: water-based polyurethane 78 wt%, color paste wt 14%, matting powder 0.5%, film-forming aid (dipropylene glycol methyl ether) wt3.8%, defoamer (water-based molecular grade defoamer) 0.18 wt %, wetting agent (alkyne glycol ethoxylate) 0.37 wt %, thickener (water-based polyurethane thickener) 0.37 wt %, and the rest is water.
[0056] Coating preparation method:
[0057] Step 1. Add 140 grams of color paste to 780 grams of pure water-based polyurethane paint (APU-390), stir and mix well;
[0058] Step 2. Add 5 grams of matting powder to the system in step 1, and mix well.
[0059] Step 3. Mix 38 grams of film-forming aids and 27.8 grams of water into the system of step 2, stir and mix evenly.
[0060] Step 4. Add 1.8 grams of defoamer to the system in step 3, stir and mix evenly.
[0061]Step 5. Add 3.7 grams of wetting agent to the system in step 4, stir and mix well.
[0062] Step 6. Add 3.7 grams of thickener to the system in step 5, stir and...
Embodiment 3
[0068] Coating material ratio: water-based polyurethane 86.5 wt %, color paste 5 wt %, coalescent (dipropylene glycol methyl ether) 4 wt %, defoamer (water-based molecular grade defoamer) 0.35 wt %, wetting agent (Alkyne glycol ethoxylate) 0.4 wt %, thickener 0.4 (Alkyne glycol ethoxylate) wt %, and the rest is water.
[0069] Coating preparation method:
[0070] Referring to Example 1.
[0071] Spraying molding method of coating material on PVC skin:
[0072] Referring to Example 1.
[0073] Results: The coating material is sprayed smoothly, the thickness of the film is uniform, the high and low temperature blasting results are qualified, the skin has no cracks and splashes, and the low temperature blasting performance of the PVC skin is significantly improved (results see Figure 5 , Figure 6 ).
PUM
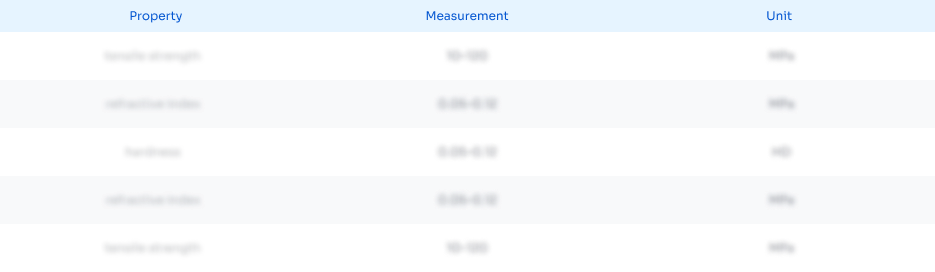
Abstract
Description
Claims
Application Information

- R&D
- Intellectual Property
- Life Sciences
- Materials
- Tech Scout
- Unparalleled Data Quality
- Higher Quality Content
- 60% Fewer Hallucinations
Browse by: Latest US Patents, China's latest patents, Technical Efficacy Thesaurus, Application Domain, Technology Topic, Popular Technical Reports.
© 2025 PatSnap. All rights reserved.Legal|Privacy policy|Modern Slavery Act Transparency Statement|Sitemap|About US| Contact US: help@patsnap.com