A preparation method of a silicon-containing macroporous alumina carrier and a hydrogenation treatment catalyst
A macroporous alumina and carrier technology, applied in the field of hydrogenation, can solve the problems of collapse, reduction of pore volume and macropore content, and the need to further improve the mechanical strength of alumina carrier.
- Summary
- Abstract
- Description
- Claims
- Application Information
AI Technical Summary
Problems solved by technology
Method used
Image
Examples
Embodiment 1
[0030] Weigh 200 g of pseudo-boehmite (produced by Shandong Aluminum Co., Ltd.) and place it in a beaker, add 400 mL of xylitol aqueous solution with a mass concentration of 25% to the beaker and soak for 4 hours. The impregnated material is filtered, and the filter cake is transferred to a high-pressure reactor for carbonization treatment at a temperature of 140°C and a treatment time of 10 hours.
[0031] Take by weighing 25 grams of carbon black powder and place it in a spray-soaked rolling pan, and in a rotating state, spray and immerse the carbon black powder in the rolling pan in an unsaturated ethanol containing 2 grams of silicon dioxide in an unsaturated spraying manner. Solution 7.5ml. The impregnated carbon black powder is fully mixed with 150 grams of the above-mentioned pseudo-boehmite and 2 g of turnip powder, and an appropriate amount of aqueous solution containing 2 g of acetic acid is added to the above materials, kneaded evenly, and extruded into strips. The...
Embodiment 2
[0033] Same as Example 1, except that pseudo-boehmite was impregnated with a mixed aqueous solution of sorbitol and mannitol with a mass concentration of 40% and a mass ratio of 1:1 for 3 hours. The carbonization treatment temperature is 130°C, and the treatment time is 14 hours. The add-on of carbon black powder is 20 grams, what used when spraying and soaking carbon black powder is the ethanol solution of the methyl orthosilicate of 7ml containing silicon dioxide 3 grams. The calcination temperature under nitrogen atmosphere was 350°C. The alumina carrier A2 of the present invention was obtained, and the properties of the carrier are shown in Table 1.
Embodiment 3
[0035] Same as Example 1, except that pseudoboehmite was impregnated for 5 hours with a mixed aqueous solution of glucose and ribose with a mass concentration of 30% and a mass ratio of 1:1. The carbonization treatment temperature is 120° C., and the carbonization treatment time is 16 hours. The add-on of carbon black powder is 35 grams, and what used when spraying and soaking carbon black powder is the ethanol solution of the butyl orthosilicate of 14ml containing silicon dioxide 5 grams, and the roasting temperature under nitrogen atmosphere is 450 ℃. The alumina carrier A3 of the present invention was obtained, and the properties of the carrier are shown in Table 1.
PUM
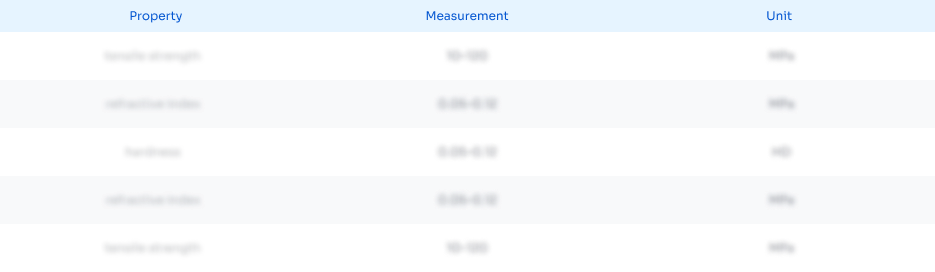
Abstract
Description
Claims
Application Information

- R&D
- Intellectual Property
- Life Sciences
- Materials
- Tech Scout
- Unparalleled Data Quality
- Higher Quality Content
- 60% Fewer Hallucinations
Browse by: Latest US Patents, China's latest patents, Technical Efficacy Thesaurus, Application Domain, Technology Topic, Popular Technical Reports.
© 2025 PatSnap. All rights reserved.Legal|Privacy policy|Modern Slavery Act Transparency Statement|Sitemap|About US| Contact US: help@patsnap.com