Fast investment casting technology of stainless steel impeller employing 3D printing solid mould
A 3D printing and rapid casting technology, which is applied in the manufacture of tools, casting molding equipment, casting molds, etc., can solve the problems of increasing the burden on enterprises, the production process of investment precision casting process, and the residue of mold shells, etc., so as to improve production efficiency , shorten the production cycle, reduce the effect of manufacturing costs
- Summary
- Abstract
- Description
- Claims
- Application Information
AI Technical Summary
Problems solved by technology
Method used
Examples
Embodiment 1
[0020] The rapid investment casting process of the stainless steel impeller using 3D printing solid model includes the following steps:
[0021] (1) On the 3D printed real model, the position where the inner gate is to be welded is punched out, and then the vent hole is sealed with ordinary wax. The 3D printed real model can be purchased directly from the 3D model manufacturer, and its material is SLS wax powder base or SLA resin base, the ordinary wax is made of the same material as candles, and can be melted in hot water at (90~95) °C;
[0022] (2) Welding the 3D printed solid model obtained through step (1) with the investment model group forming the gating riser system to form a module;
[0023] (3) The surface of the module obtained in step (2) is coated with modified silica sol with a silica sol content of 10%, and the modified silica sol forms an integral shell coated on the surface of the module after drying and hardening. Compared with ordinary silica sol, the modifi...
Embodiment 2
[0031] The rapid investment casting process of the stainless steel impeller using 3D printing solid model includes the following steps:
[0032] (1) On the 3D printed real model, the position where the inner gate is to be welded is punched out, and then the vent hole is sealed with ordinary wax. The 3D printed real model can be purchased directly from the 3D model manufacturer, and its material is SLS wax powder base or SLA resin base, the ordinary wax is made of the same material as candles, and can be melted in hot water at (90~95) °C;
[0033] (2) Welding the 3D printed solid model obtained through step (1) with the investment model group forming the gating riser system to form a module;
[0034] (3) The surface of the module obtained in step (2) is coated with modified silica sol with a silica sol content of 10%, and the modified silica sol forms an integral shell coated on the surface of the module after drying and hardening. Compared with ordinary silica sol, the modifi...
Embodiment 3
[0042] The rapid investment casting process of the stainless steel impeller using 3D printing solid model includes the following steps:
[0043] (1) On the 3D printed real model, the position where the inner gate is to be welded is punched out, and then the vent hole is sealed with ordinary wax. The 3D printed real model can be purchased directly from the 3D model manufacturer, and its material is SLS wax powder base or SLA resin base, the ordinary wax is made of the same material as candles, and can be melted in hot water at (90~95) °C;
[0044] (2) Welding the 3D printed solid model obtained through step (1) with the investment model group forming the gating riser system to form a module;
[0045] (3) The surface of the module obtained in step (2) is coated with modified silica sol with a silica sol content of 10%, and the modified silica sol forms an integral shell coated on the surface of the module after drying and hardening. Compared with ordinary silica sol, the modified...
PUM
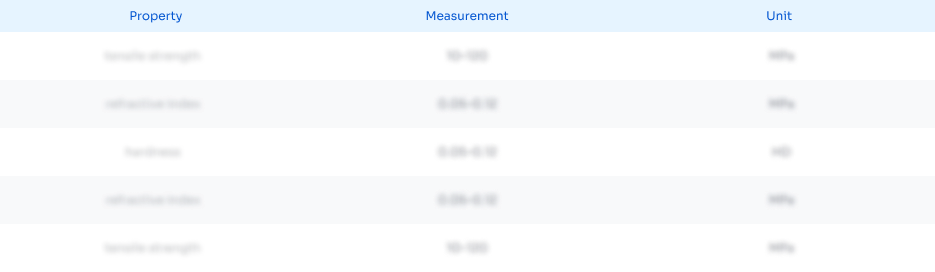
Abstract
Description
Claims
Application Information

- R&D Engineer
- R&D Manager
- IP Professional
- Industry Leading Data Capabilities
- Powerful AI technology
- Patent DNA Extraction
Browse by: Latest US Patents, China's latest patents, Technical Efficacy Thesaurus, Application Domain, Technology Topic, Popular Technical Reports.
© 2024 PatSnap. All rights reserved.Legal|Privacy policy|Modern Slavery Act Transparency Statement|Sitemap|About US| Contact US: help@patsnap.com