Preparation method of indium trichloride
A technology of indium trichloride and chlorine gas, which is applied in chemical instruments and methods, inorganic chemistry, gallium/indium/thallium compounds, etc., can solve the problems of insufficient chlorination, containing, difficult to control the reaction, etc., and achieve high utilization rate of raw materials , short process time and low production cost
- Summary
- Abstract
- Description
- Claims
- Application Information
AI Technical Summary
Problems solved by technology
Method used
Examples
preparation example Construction
[0016] The preparation method of a kind of indium trichloride of the present invention comprises the following steps: primary chlorination: passing protective gas into the first reactor to replace the air in the first reactor, placing the raw material indium in the first reactor and heating to The first heating temperature makes the raw material indium melt, and the dry chlorine gas is passed into the liquid indium at a flow rate of 60~600L / h during the first aeration time to react. The first aeration time is proportional to the mass of the raw material indium, and then the aeration is stopped. Dry the chlorine gas, cool to room temperature to obtain solid indium chloride, and demold the indium chloride for use.
[0017] Secondary chlorination: put solid indium monochloride into a second reactor, pass through protective gas to replace the air in the second reactor, then stop feeding protective gas and change to dry chlorine gas, dry chlorine gas to The ventilation flow rate of...
Embodiment 1
[0026] Primary chlorination: Take 2kg of 4N indium, melt it in an indium melting furnace, transfer it to an indium chloride reactor, feed dry nitrogen at a certain flow rate to discharge the oxygen in the reactor, heat to 230°C, and turn off the nitrogen , feed dry chlorine gas at a rate of 60 L / h for 200 minutes, transfer indium monochloride to a graphite mold after the reaction, and cool to room temperature.
[0027] Secondary chlorination: put 2.6kg of indium chloride into the heating end of the quartz chlorination sublimation reactor, feed dry nitrogen at a certain flow rate to discharge the air in the reactor, close the nitrogen gas and feed dry chlorine gas, the flow rate is 60L / h , the temperature was raised to 300° C., and the indium chloride at the heating end was completely reacted. After cooling down to room temperature, 3.8 kg of anhydrous indium trichloride was collected at the collecting end. Sampling test shows that the product has a purity of 99.999% and a wate...
Embodiment 2
[0029] Primary chlorination: take 2kg of 4N indium, melt it in an indium melting furnace, transfer it to an indium chloride reactor, feed dry nitrogen at a certain flow rate to discharge the oxygen in the reactor, heat to 400°C, and turn off the nitrogen , feed dry chlorine gas at a rate of 300 L / h for 40 minutes, transfer indium monochloride to a graphite mold after the reaction, and cool to room temperature.
[0030] Secondary chlorination: put 2.6kg of indium chloride into the heating end of the quartz chlorination sublimation reactor, feed dry nitrogen at a certain flow rate to discharge the air in the reactor, close the nitrogen gas and feed dry chlorine gas, the flow rate is 300L / h , the temperature was raised to 500° C., and the indium chloride at the heating end was completely reacted. After cooling down to room temperature, 3.8 kg of anhydrous indium trichloride was collected at the collecting end. Sampling test shows that the product has a purity of 99.999% and a wat...
PUM
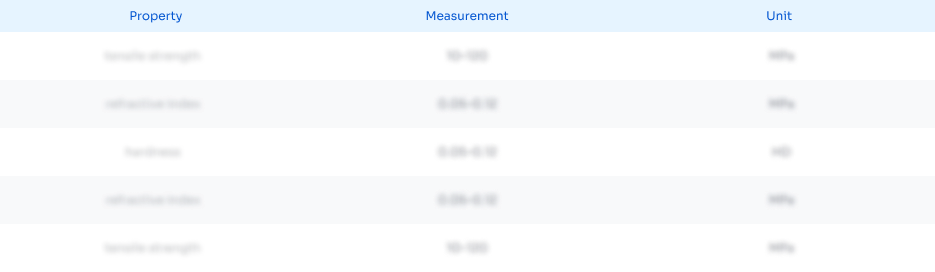
Abstract
Description
Claims
Application Information

- R&D
- Intellectual Property
- Life Sciences
- Materials
- Tech Scout
- Unparalleled Data Quality
- Higher Quality Content
- 60% Fewer Hallucinations
Browse by: Latest US Patents, China's latest patents, Technical Efficacy Thesaurus, Application Domain, Technology Topic, Popular Technical Reports.
© 2025 PatSnap. All rights reserved.Legal|Privacy policy|Modern Slavery Act Transparency Statement|Sitemap|About US| Contact US: help@patsnap.com