Method for compensating cutting error of hard-brittle material thin-walled component
A technology for thin-walled parts and error compensation, applied in the field of patent classification G05 control, which can solve problems such as poor processing technology, affecting processing quality, and inability to completely eliminate errors
- Summary
- Abstract
- Description
- Claims
- Application Information
AI Technical Summary
Problems solved by technology
Method used
Image
Examples
Embodiment Construction
[0026] In order to make the purpose, technical solutions and advantages of the embodiments of the present invention more clear, the technical solutions in the embodiments of the present invention are clearly and completely described below in conjunction with the drawings in the embodiments of the present invention:
[0027] Such as Figure 1-5 Shown: a processing error compensation method for thin-walled parts, which mainly includes the following steps:
[0028] For a specific thin-walled part, according to the material used in the thin-walled part, a cutting force model for cutting the material is established, and the cutting force model must include the radial depth of cut a e This parameter, other parameters can also be included, but not mandatory.
[0029] F=f(a e )
[0030] Among them: F stands for cutting force, a e represents the radial depth of cut;
[0031] Considering that the last process is a finishing process, adding error compensation to the last process can...
PUM
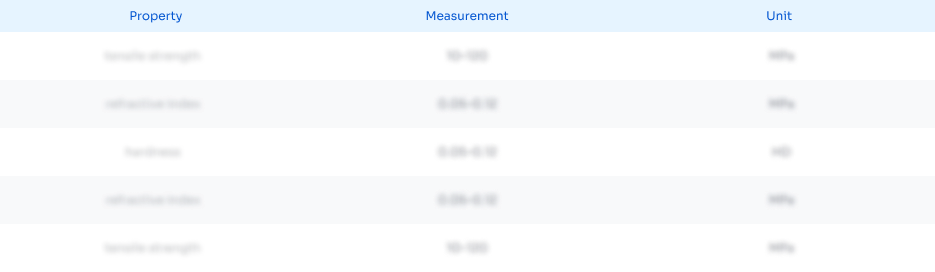
Abstract
Description
Claims
Application Information

- R&D Engineer
- R&D Manager
- IP Professional
- Industry Leading Data Capabilities
- Powerful AI technology
- Patent DNA Extraction
Browse by: Latest US Patents, China's latest patents, Technical Efficacy Thesaurus, Application Domain, Technology Topic, Popular Technical Reports.
© 2024 PatSnap. All rights reserved.Legal|Privacy policy|Modern Slavery Act Transparency Statement|Sitemap|About US| Contact US: help@patsnap.com